Guida alle metriche e i KPI manutenzione
Metriche e KPI manutenzione sono elementi essenziali per riuscire a monitorare le performance dei nostri asset e del team di manutenzione. In questo articolo offriamo una panoramica completa sulle principali metriche e KPI, spiegando come sceglierli in relazione ai nostri obiettivi e come calcolarle nel modo più semplice.
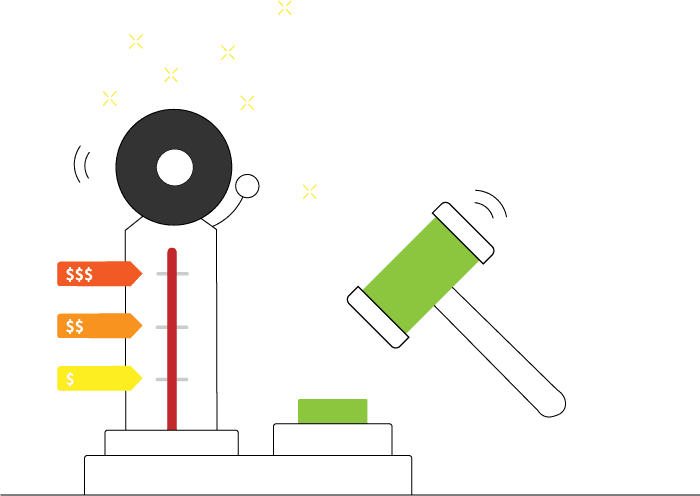
Condividi l’articolo
Contenuto dell'articolo
Cos’è un KPI di manutenzione. L’anatomia dei dati
KPI vs Metriche di manutenzione. Qual è la differenza?
Adottare una logica di miglioramento continuo
Il nostro approccio alle metriche e KPI di manutenzione
Metriche e KPIs legati al Service Management
Metriche e KPIs legati all’Asset Management
Metriche e KPIs legati al Controllo dei costi
Guida alle metriche e ai KPIs di manutenzione
- Numero di fermi macchina
- Top Worst Assets
- Backlog di manutenzione
- Wrench time
- Mean Time Between Failure
- Mean Time To Repair
- Mean Time To Failure
- % di OdL correttivi/pianificati chiusi entro il periodo definito
- Trend Ordini di lavoro creati
- Overall equipment effectiveness
- Costo totale della manutenzione correttiva
- Costo totale della manutenzione preventiva
- Peso in % della manutenzione correttiva su quella pianificata
- Peso in % dell’utilizzo delle risorse interne su quelle esterne
Smetti di guidare al buio
Immagina di guidare un’auto che non abbia la spia del livello di carburante. O che sia priva del tachimetro. Per conoscere la velocità a cui stai andando saresti costretto a contare uno per uno i chilometri fatti e dividere il totale per il tempo che hai impiegato a percorrerli. E anche così sarebbe una rilevazione estremamente approssimativa.
Adesso immagina di dover guidare questa stessa auto ogni giorno, per otto ore. Sarebbe un caos totale, non è così? Il serbatoio continuamente a secco e multe per eccesso di velocità diventerebbero la norma e tutto questo perché stai guidando al buio.
Ecco, adesso prova a pensare di gestire i tuoi impianti, o addirittura un’intera facility in questo modo.
Per farla breve, è impossibile riuscire a migliorare ciò che non puoi misurare.
Per fortuna però ci sono alcune metriche e KPI possono darti una mano, proprio come il tachimetro o la spia del carburante della tua auto, a raggiungere il successo.
Le metriche e i KPI manutenzione ti permettono di fare luce su qualsiasi processo e operazione si svolga all’interno della tua facility. La parte migliore è che queste metriche non sono così complicate da calcolare e monitorare, almeno se hai a disposizione il tool giusto, al momento giusto. La parte ancora migliore però, è che – nonostante tutto – ad oggi ci sono ancora molte aziende che non si prendono la briga di fare questo tipo di analisi in modo serio e costante, limitandosi spesso ad acquisire dati approssimativi e processandoli in modo inefficiente. Ciò rappresenta un’ottima possibilità per riuscire ad acquisire un vantaggio competitivo rispetto alla concorrenza.
Vuoi scoprire di più sulle metriche e KPI di manutenzione?
Cos’è un KPI manutenzione: l’anatomia dei dati
I KPI (key performance indicators) sono indicatori di prestazione, cioè misurazioni che, attraverso il loro monitoraggio, ci danno un’indicazione precisa del nostro lavoro rispetto agli obiettivi che ci siamo posti. Possiamo così misurare le performance di una persona, di un asset, di un processo o di un’azienda intera e quanto sono efficienti nel raggiungere gli obiettivi stabiliti.
In manutenzione, possono per esempio essere utilizzati per stabilire nuove strategie che riducano al minimo i fermi macchina, individuare colli di bottiglia e inefficienze, costruire piani di manutenzione preventiva migliori e ottimizzare i costi.
In altre parole, i KPI servono a mostrarti la via, ad accendere i fanali della tua auto, facendo luce sui processi e aiutandoti a disegnare la strada più veloce per raggiungere gli obiettivi che hai scelto.
“La misurazione è il primo passo che porta al controllo e infine al miglioramento. Se non riesci a misurare qualcosa, non puoi capirlo. Se non riesci a capirlo, non puoi controllarlo. Se non riesci a controllarlo, non puoi migliorarlo.”
– James Harrington
KPI Vs Metriche di manutenzione. Qual è la differenza?
Metriche e KPI manutenzione sono due termini spesso utilizzati come sinonimo. In ogni caso, esiste una sottile differenza tra loro.
Nello specifico, i KPI sono numeri che ci servono per dare una dimensione ai nostri progressi in relazione agli obiettivi che abbiamo stabilito. Ci servono per fissare un obiettivo a cui vogliamo tendere.
Le metriche sono invece i mattoncini con cui costruiamo i KPI e servono a connettere le nostre azioni alle performance che vogliamo monitorare.
KPI esempio:
Mettiamo che il tuo obiettivo sia quello di incrementare i ricavi a fine anno. Per raggiungere questo obiettivo, vorrai aumentare il volume di merce prodotta e venduta.
La capacità produttiva è però strettamente influenzata dal numero di fermi macchina riscontrati. Dunque, uno dei KPI che ti interesserà monitorare sarà appunto il numero totale di fermi macchina o, ancora meglio, il tempo totale di fermo macchina relativo ad un determinato impianto.
Tutte le azioni che sono collegate a questo KPI e possono essere quantificate, dal numero di interventi di manutenzione correttiva fino al tempo operativo tra due guasti, rappresentano metriche di manutenzione da monitorare.
Adottare una logica di miglioramento continuo
Avrai senz’altro sentito parlare di TPM – Total Productive Maintenance. Ma cosa c’entra il TPM con il monitoraggio dei KPI aziendali e le metriche di manutenzione?
Come tutte le politiche attive di manutenzione, il TPM tenta di risolvere i problemi legati alla diminuzione del rendimento di macchine e impianti e rendere più efficienti i processi legati alla gestione degli asset. L’obiettivo finale del TPM è dunque quello di incrementare la produttività generale attraverso l’ottimizzazione di questi processi.
Ma come si può migliorare un processo se non si è in grado di monitorarlo? Qualsiasi azione tu compia, senza un riscontro tangibile, non ti permette di individuare e scindere in modo chiaro e preciso ciò che funziona da ciò che invece non funziona.
Il nostro approccio alle metriche e KPI manutenzione
Questo articolo è focalizzato sulle metriche e i KPI manutenzione. Metriche e KPI ti dicono molto sul come e sul perché dietro ad ogni evento, fornendoti un prezioso strumento di diagnosi volto al miglioramento delle tue operazioni e dei risultati dell’intera azienda. Ma riuscire a monitorare questi indicatori di performance ha un costo, se non altro in termini di tempo e di risorse da dedicare loro. Ecco perché è importante riuscire a scegliere i KPI che ci interessano e focalizzarsi su di essi.
Per scegliere quali metriche e KPI fanno al caso tuo, occorre partire dagli obiettivi finali che intendi raggiungere. Per obiettivi, devono essere intesi soltanto aspetti che siano misurabili. Una volta definiti gli indicatori KPI a cui si vuole tendere, sarà più facile capire cosa è necessario monitorare.
Per esperienza sappiamo che la scelta di questi obiettivi molto spesso si rivela tutt’altro che semplice.
Per semplificare questo processo mainsimWay, il nostro personale approccio all’implementazione di un CMMS, raggruppa questi obiettivi in tre macro categorie, ciascuna delle quali contiene al suo interno un gruppo di indicatori.
Quali sono queste categorie?
- Service Management
- Asset Management
- Controllo dei costi
Vediamole insieme nel dettaglio.
“Come possiamo migliorare un processo se non possiamo misurarlo?”
Metriche e KPI legati al Service Menagement
I KPIs e le metriche legate al Service sono indicatori particolarmente adatti al settore Facility Management e Global Service, ma non solo. Gli stessi indicatori possono essere applicati anche in ambienti industriali, laddove si intende misurare il servizio di manutenzione.
Attraverso questo gruppo di KPI, il responsabile della manutenzione potrà rispondere a domande quali:
- Quanto è performante il sistema di gestione delle richieste di intervento?
- Quanto è performante il processo di gestione degli interventi programmati?
- Quanti/quali ordini di lavoro sono rimasti incompiuti?
- Quanto tempo intercorre tra l’effettivo momento del guasto e la sua segnalazione?
- Il processo gestionale presenta dei colli di bottiglia?
Quali sono i KPI di manutenzione relativi al Service management?
- % di Ordini di Lavoro (OdL) correttivi chiusi entro un periodo definito
- % OdL pianificati chiusi entro un periodo definito
- Backlog di manutenzione (numero di OdL arretrati)
- Trend OdL creati: manutenzione correttiva Vs manutenzione pianificata
- OdL suddivisi per gruppo
- OdL suddivisi per categoria
Metriche e KPI manutenzione legati all’Asset Management
Il secondo gruppo, Asset Management, si riferisce a metriche e KPI che hanno come obiettivo principale quello di monitorare una serie di valori che sono propri dell’ingegneria della manutenzione. Sono indicatori che consentono di portare la manutenzione ad un livello di maggior conoscenza e professionalità, spesso utilizzati in ambiente industry e manufacturing dove si hanno macchinari e impianti da monitorare.
Attraverso questi indicatori potrai rispondere a indagini quali:
- Quanto tempo intercorre tra due anomalie consecutive sul medesimo asset (MTBF)?
- Quanto tempo è mediamente necessario per la risoluzione di un’anomalia su uno specifico asset (MTTR)?
- Quali sono gli asset che hanno presentato più anomalie (Top Worst Asset)?
- Qual è il tempo di ogni singola riparazione (MRT – Wrench Time)
Quali sono i KPI di manutenzione relativi all’Asset Management?
- Mean Time Between Failures (MTBF)
- Mean Time To Repair (MTTR)
- Mean Time To Failure (MTTF)
- Mean Repair Time (MRT)
- Mean Time Between Maintenance (MTBM)
- Numero Totale di Fermi Macchina
- Top Worst Assets (Peggiori assets in termini di performance)
Metriche e KPI manutenzione legati al controllo dei costi
Il terzo gruppo, Controllo dei Costi, si riferisce a metriche e KPI che hanno come obiettivo una definizione dei costi che incidono sulla manutenzione. I costi possono essere dettati dal tipo di manutenzione effettuato, dall’utilizzo di risorse interne o esterne (fornitori, aziende di servizi) e dai materiali impiegati.
Tramite l’analisi di questi KPI è possibile rispondere alle seguenti domande:
- Quanto è costata la manutenzione, durante un determinato periodo, per uno specifico asset?
- Quanto ha inciso la manodopera sul costo totale della manutenzione
- Quanto ha inciso il costo dei materiali di ricambio sul costo totale?
Questi KPI rappresentano l’obiettivo finale di una conduzione della manutenzione, ma naturalmente richiedono una certa accuratezza nell’identificazione delle voci di costo associate agli interventi.
Quali sono i KPI di manutenzione relativi al controllo dei costi?
- Costo totale della manutenzione correttiva
- Costo totale della manutenzione pianificata
- Peso in % della manutenzione correttiva su quella pianificata
- Peso in % dell’utilizzo di risorse esterne sulle risorse interne
Guida alle metriche e ai KPI di manutenzione
Adesso che abbiamo una visione più precisa di cosa possiamo misurare in relazione ai nostri obiettivi, è finalmente giunto il momento di esplorare una per una queste metriche e KPIs. Di seguito, proponiamo una panoramica dettagliata dei principali indicatori, con annesse formule per il calcolo, World Class Standard e qualche suggerimento su come riuscire a migliorarne i risultati.
Ovviamente ciascuna di queste metriche può essere calcolata anche a mano, a patto però di riuscire a tracciare correttamente i processi e avere a disposizione dati precisi e attendibili.
Se invece disponete già di un buon software CMMS (Computerized Maintenance Management System) è molto probabile che stiate già tracciando almeno alcune di queste metriche e KPIs che, in base agli obiettivi scelti, sono fornite in modo automatico dal sistema.
Al fianco di ogni KPI trovate poi un riferimento a quale categoria appartiene delle tre che abbiamo descritto nel capitolo precedente.
Numero di fermi macchina
Monitorare il numero di fermi macchina rappresenta spesso l’entry level nella gestione e nell’analisi dei KPI aziendali.
Quando ci si riferisce al numero di fermi macchina, essi possono essere il risultato sia di una manutenzione non pianificata, come per esempio il guasto ad un impianto o la rottura di un componente che necessita l’arresto del macchinario per essere aggiustato, sia le fermate pianificate, che di solito corrispondono ad un’attività di manutenzione preventiva.
Questo KPI è molto utile per comprendere quali sono gli asset che inficiano in maniera predominante sul processo produttivo e su quello manutentivo.
Individuando tali asset, è possibile indagare sulle cause principali di guasto (Root Causes Analysis) per comprendere se, ad esempio, sono presenti difetti congeniti associabili allo specifico asset, come errori di progettazione.
Perché è importante tracciare il numero di fermi macchina?
Tracciare il numero di fermi macchina riportati, specialmente in un’azienda produttiva, è particolarmente importante per alcune semplici ragioni.
Avere un’idea piuttosto precisa della disponibilità dei propri asset, significa disporre di uno strumento di diagnosi e un indicatore di prestazione valido sia dal lato manutentivo che da quello della produzione. Per esempio, un alto tasso di fermi macchina potrebbero significare che il piano di manutenzione preventiva scelto non sta funzionando nel modo in cui avevamo previsto, o che qualcosa non funziona nel processo di produzione.
Inoltre, restringendo il campo a singole aree, come per esempio una specifica linea produttiva, potremo sapere in modo ancora più preciso dove risiede il problema e concentrare gli sforzi per capire cosa non sta funzionando a dovere.
Top Worst Assets (Peggiori asset)
Un software CMMS, ti permette in ogni momento di consultare la lista degli asset che hanno avuto più guasti in un determinato periodo di tempo, in modo da aiutarti ad individuare immediatamente quali sono gli assets su cui dovrebbe concentrarsi la tua attenzione, ad esempio attuando o perfezionando politiche di manutenzione programmata che siano mirate in funzione delle cause radice dei problemi riscontrati con maggiore frequenza.
Questa lista dei peggiori asset, che in mainsim trovi direttamente sulla dashboard principale, è ordinata in base alla criticità degli asset e ti permette di focalizzare l’attenzione sugli asset che presentano più problematiche, ad esempio attuando delle politiche di manutenzione programmata mirate in funzione delle cause radice dei problemi riscontrati con maggiore frequenza.
MainTIPS
La lista dei Top Worst Assets in mainsim si trova direttamente sulla dashboard principale in modo che sia consultabile nel modo più semplice e rapido.
Inoltre, poiché gli asset non sono tutti uguali in termini di importanza, questa lista è ordinata in base alla loro criticità.
Asset Management
Backlog di manutenzione (Ordini di lavoro arretrati)
Per garantire una performante gestione degli ordini di lavoro e quindi di riflesso attuare una logica di miglioramento continuo dei KPI manutenzione, è necessario avere una visione accurata del lavoro rimasto in arretrato.
Ad esempio, se una richiesta di intervento è stata inserita nel processo ma non viene gestita da nessuno, è molto importante averne evidenza in quanto con il passare del tempo il guasto segnalato potrebbe generare ulteriori problemi. Inoltre, attraverso questo KPI possiamo fare luce su eventuali problemi di allocazione delle nostre risorse.
Va da sé però che non tutti gli ordini di lavoro e le richieste di intervento hanno la stessa importanza o sono ugualmente urgenti. Fare chiarezza in questo può non essere semplice senza uno strumento, come il CMMS, che sia in grado di suddividere gli ordini di lavoro per livello di priorità in base, per esempio, alla criticità dell’asset.
Detto questo, è chiaro che avere un certo numero di ordini di lavoro arretrati è del tutto normale. Lo scopo del monitoraggio di questo KPI manutenzione non dovrebbe essere quello di eliminare completamente il backlog di manutenzione, ma di tenere questo numero entro una soglia accettabile, che sia dunque gestibile dal team di tecnici a disposizione.
Inoltre, potrebbe essere importante stabilire quale parte di questi ordini di lavoro arretrati rientrino in un processo di manutenzione preventiva e quali in uno di manutenzione a guasto (correttiva).
MainTIPS
Mainsim ti permette di tenere il conteggio degli ordini di lavoro rimasti da gestire sempre sott’occhio, grazie ad un semplicissimo grafico a torta posto sulla dashboard principale del CMMS. Inoltre, il sistema è in grado di mostrare l’elenco per età e priorità decrescenti, dando risalto agli ordini di lavoro più anziani aventi maggiore priorità.
Wrench Time (Tempo di riparazione)
Spesso considerata come una metrica e un KPI minore, non così importante nella valutazione dei processi di manutenzione, il tempo di riparazione (in inglese Wrench Time) può fornire invece delle informazioni molto importanti per scovare colli di bottiglia e migliorare il workflow.
Abbiamo parlato in modo approfondito del Wrench Time in questo articolo interessantissimo che abbiamo tradotto dall’originale.
MainTIPS
Con mainsim mobile è possibile spingersi ad un grado ulteriore di dettaglio nell’analisi dei tempi di manutenzione, misurando con precisione il tempo che le persone impiegano nell’eseguire la riparazione grazie al tasto Rec&Stop disponibile sull’app mobile.
Service Management
Mean Time Between Failures – MTBF
Il tempo medio tra guasti
Il Mean Time Between Failure (MTBF) rappresenta il tempo medio che intercorre tra il verificarsi di un guasto e quello successivo. Stiamo parlando dunque di una metrica strettamente correlata alla disponibilità di un macchinario o di un impianto.
La disponibilità (Uptime) di un asset, è anche uno dei principali KPI manutenzione per il calcolo dell’OEE (Overall Equipment Effectiveness) e può essere considerata una metrica fondamentale per chiunque intenda monitorare la produzione.
Formula
MTBF = Total Uptime / # di fermi macchina
Come migliorare il MTBF
Migliorare l’MTBF è uno degli obiettivi più comuni quando si ha a che fare con la produzione. Tenere traccia dell’indice KPI relativo al tempo medio tra i guasti, ci permette di pianificare le nostre attività in modo più preciso. Il primo step per migliorare l’MTBF è quello di assicurarsi che i dati siano registrati nel modo più accurato possibile. In questo senso, la disponibilità di un CMMS gioca un ruolo fondamentale.
Il secondo step è quello di investire tempo e risorse in audit e controlli preventivi, in modo tale da tenere in ordine i propri macchinati anche con logiche di miglioramento continuo e TPM (Total Productive Maintenance).
MainTIPS
A volte può essere complicato riuscire ad individuare il modo corretto per calcolare l’MTBF. Per questo mainsim mette a disposizione un report sempre aggiornato all’interno del quale, insieme a tante altre metriche e KPI manutenzione, puoi trovare anche il valore MTBF di ogni asset. Prova a confrontare questo valore con quello indicato dal produttore del macchinario per capire se ci sono incongruenze e valutare meglio possibili interventi.
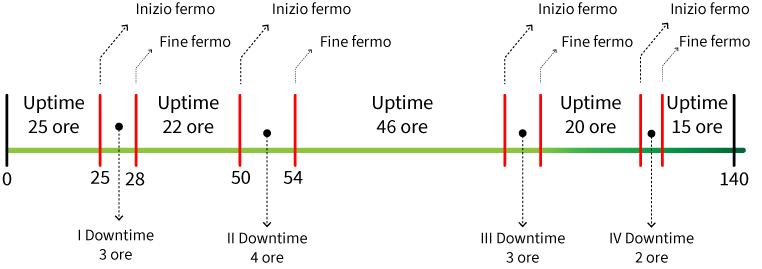
Mean Time To Repair (MTTR)
Il tempo medio di riparazione
Il Mean Time To Repair (MTTR) indica il tempo medio intercorso tra la data di inizio e la data di fine intervento. Pertanto, è una metrica di manutenzione correlata alla disponibilità di un asset.
Quando un macchinario subisce un arresto, specialmente se dovuto ad un guasto imprevisto, questo impatta negativamente sulla sua disponibilità: il numero di ore, cioè, che lo stesso impianto resta operativo e disponibile alla produzione.
Gestendo le proprie operazioni in modo proattivo e adottando un mindset data-driven, si possono ridurre sensibilmente i tempi di riparazione e le perdite di produttività.
Formula
MTTR = Tempo totale di fermo macchina / # di fermate
Come migliorare l’indicatore MTTR
Il metodo migliore per ridurre l’MTTR è senz’altro quello di ricorrere all’analisi delle cause radice di un guasto. Monitorando attentamente i dati di ciascun asset, è infatti possibile individuare possibili cause di guasto in anticipo. Con un moderno software manutenzione CMMS, è possibile infatti analizzare nel dettaglio le cause che portano ai guasti frequenti attraverso la Root Cause Analysis.
Un altro modo ugualmente efficace per ridurre questo valore, è rappresentato dalla manutenzione preventiva, in modo tale da rilevare eventuali problematiche prima che si trasformino in guasti più seri. Questo atteggiamento proattivo nei confronti dei propri asset si ripercuote positivamente sul valore MTTR
MTTR e World Class Standard
Molto dipende dal tipo di asset e dalla sua età, ma il World Class Standard individua intorno alle 5 ore un buon valore MTTR.
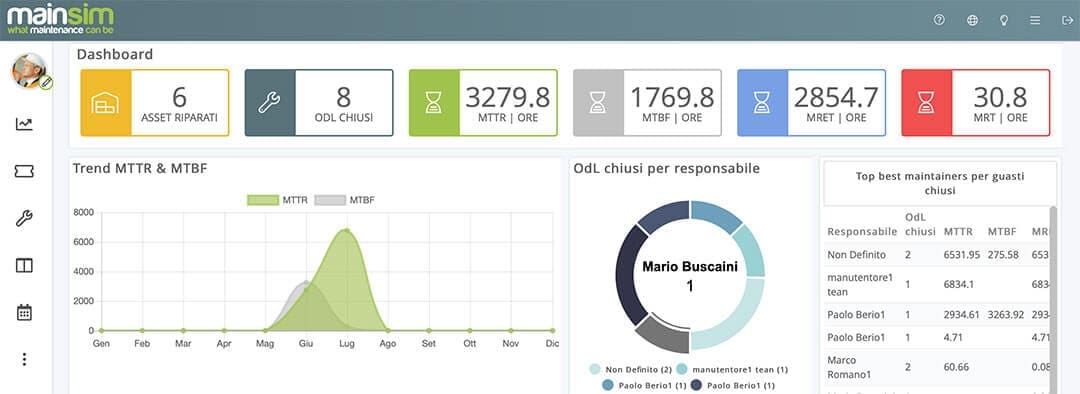
Particolare della dashboard di mainsim dedicata al monitoraggio di metriche e KPI manutenzione. Il calcolo di questi indicatori viene svolto in automatico dal sistema.
Mean Time To Failure (MTTF)
Il tempo medio all’insorgere di un guasto
Il MTTF (Mean Time To Failure), è un KPI manutenzione che indica il tempo medio all’insorgere di un guasto. Si tratta dunque di un indicatore di prestazione legato all’affidabilità dei componenti o di un asset e rappresenta la sua durata media.
Attenzione però: l’MTTF è una misurazione valida soltanto per quegli assets che non sono sottoposti ad un processo di manutenzione e vengono sostituiti una volta che si sono guastati.
Per assets più complessi, che al contrario possono essere riparati, è preferibile rifarsi ad altre metriche come MTTR e MTBF.
Formula
MTTF = Totale ore operative / Numero Totale di Asset in uso
Asset Management
% OdL Correttivi chiusi entro un dato periodo definito e % di OdL Pianifcati chiusi entro un dato periodo
La tempestività nella risoluzione delle anomalie mediante manutenzioni che possono essere correttive o pianificate rappresenta un KPI manutenzione molto importante relativo al Service, spesso utilizzato dai facility manager per valutare la compliance del team di manutenzione e dei fornitori rispetto agli ordini di lavoro creati.
Entrambi questi KPI manutenzione sono espressi in percentuale, pertanto più il dato è vicino al 100%, più il sistema è performante nella gestione delle anomalie.
Per monitorare questo KPI deve essere definito un periodo di riferimento (ad esempio 1 mese) sulla base del quale è possibile calcolare la percentuale di richieste di manutenzione correttiva/preventiva chiuse entro il periodo indicato.
Esempio di monitoraggio
Potresti stabilire come obiettivo quello di ottenere l’85% degli ordini di lavoro correttivi chiusi entro 30 giorni. Se a fine mese ottieni un valore pari al 70%, questo significa che solo il 70% degli ordini di lavoro totali è stato effettivamente chiuso nel periodo indicato. Questo indica la necessità di indagare meglio le cause di questo ritardo, dalla quantità di risorse allocate ad eventuali colli di bottiglia nel processo manutentivo.
MainTIPS
Questo genere di analisi viene svolta in modo automatico da sistema CMMS, mediante dashboard e diagrammi a torta che rendono più semplice il monitoraggio di questo KPI manutenzione.
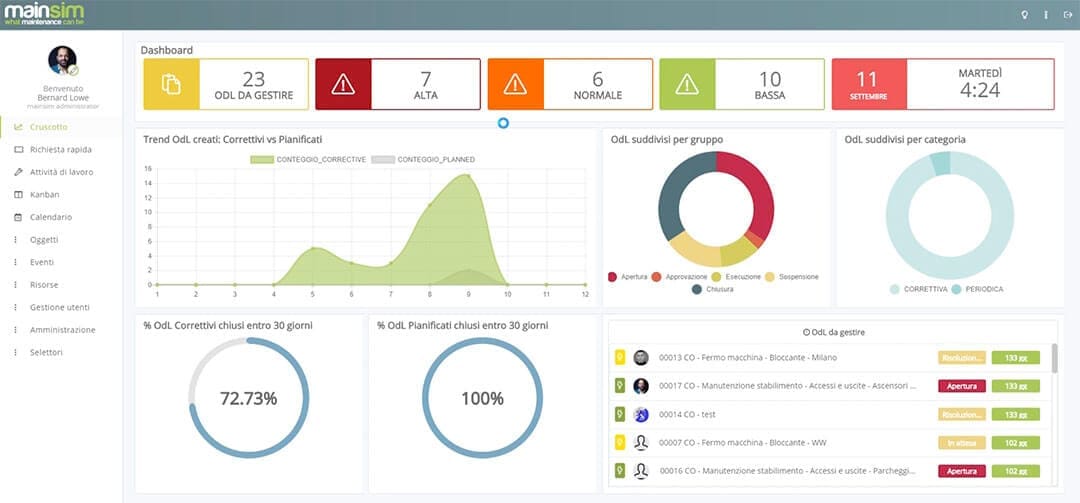
Trend OdL creati: Ordini di lavoro Correttivi Vs Ordini di lavoro Pianificati
Mediante la visualizzazione dell’andamento degli ordini di lavoro nel tempo, è possibile individuare i periodi critici nei quali solitamente si verificano più anomalie.
Analizzare il trend degli ordini di lavoro creati, confrontando quelli di tipo correttivo con quelli pianificati, è utile per ottimizzare l’uso delle risorse e capire se il nostro piano di manutenzione preventiva sta funzionando o se invece necessita di essere rivisto.
World Class Standard
Il world class standard indica come obiettivo ottimale il raggiungimento del 90% di ordini di lavoro preventivi su quelli correttivi.
Service Management
Overall Equipment Effectiveness – OEE
L’overall Equipment Effectiveness (OEE) è un indicatore standard usato per misurare l’efficacia di un impianto e le sue performance. Calcolare l’indice OEE aiuta ad identificare quali sono le aree critiche di un impianto e trovare nuove strategie di miglioramento per aumentare la capacità produttiva e migliorarne le performance.
OEE e World Class Standard
Sono tre i fattori chiave che fanno capo all’indice OEE: disponibilità, efficienza e qualità del prodotto.
È lo stesso Seiichi Nakajima, colui che ha concettualizzato e introdotto l’indicatore OEE, a identificare il World Class Standard. L’obiettivo ideale da raggiungere per ognuno di questi tre fattori è il seguente:
- Disponibilità: 90%
- Efficienza: 95%
- Qualità del prodotto: 99%
In totale, l’obiettivo minimo dovrebbe essere quello di raggiungere un OEE superiore al 77%.
Come calcolare l’indice OEE
Per calcolare questo KPI manutenzione, è necessario prima avere a disposizione i tre fattori che lo definiscono. Ecco come ricavarli.
La disponibilità
La disponibilità indica il tempo totale in cui un impianto resta disponibile alla produzione.
D = (Tempo Totale Operativo – Fermi macchina Pianificati) / Tempo Totale Operativo
Efficienza
L’efficienza quantifica quanto impiega un macchinario a completare un processo di produzione rispetto al tempo ideale di un ciclo (solitamente indicato dal produttore)
Un possibile calcolo, un po’ semplificato, è il seguente:
E = [(# unità processate * Tempo ideale di un ciclo) / Tempo effettivo di processo]
Qualità
Qualità: il tasso di qualità del prodotto identifica il numero di pezzi conformi prodotti. Per un paniere di 440 unità prodotte, se solo 435 rispettano gli standard di qualità, il tasso di qualita sarà del 97,73%
Q = (Numero di unità conformi prodotte / Totale di unità processate) *100
Formula per il calcolo dell’OEE
L’indice OEE è dunque calcolato a partire da questi tre fattori con la seguente formula:
OEE = Disponibilità * Efficienza * Qualità
Come migliorare il proprio OEE
Un buon punto di partenza per aumentare la produttività e l’efficacia del tuo impianto è quello di eliminare le Six Big Losses:
- Evitare i guasti ai macchinari
- Velocizzare il setup e gli aggiustamenti programmando gli interventi in modo efficiente
- Minimizzare le micro fermate dovute a piccole inefficienze degli impianti
- Evitare di sovraccaricare i macchinari con tempi di attività troppo lunghi
- Minimizzare i difetti di processo, cercando di diminuire il numero di pezzi prodotto non conformi allo standard richiesto
- Prevenire i periodi di produzione ridotta
Asset Management
Costo totale della manutenzione correttiva
Oltre ai KPI relativi al service e manutenzione, è importante anche riuscire a calcolare i costi e utilizzare questi riferimenti come KPI per valutare l’andamento delle operazioni di manutenzione.
Questo KPI rappresenta il costo totale imputabile ai soli interventi di manutenzione correttiva. Il costo deve tenere conto delle voci associate all’eventuale utilizzo di risorse esterne (fornitori), calcolato come acquisto di servizi terzi, oppure di risorse interne (utilizzo ore uomo del personale), oltre all’eventuale consumo di materiali di ricambio.
Costo totale della manutenzione preventiva
Attraverso l’analisi di questo KPI è possibile monitorare il costo totale imputabile ai soli interventi di manutenzione pianficata. Come il costo della manutenzione correttiva, anche questo indicatore di prestazione deve tenere conto dell’eventuale utilizzo di risorse interne ed esterne, oltre che all’eventuale consumo di materiali.
Peso in percentuale della manutenzione correttiva su quella pianificata
Questo KPI prevede di calcolare il costo espresso % della manutenzione correttiva rispetto a quella pianificata. L’obiettivo ideale sarebbe quello di annullare l’impatto dovuto ai guasti imprevisti, aumentando l’effort sulla manutenzione preventiva.
Ad esempio, se sono stati spesi 1500 euro per la manutenzione correttiva (es. ore uomo + materiali) e 500 euro per le pianificate (es. ore uomo) il KPI restituirebbe: (1500/2000)*100 = 75%
L’obiettivo è di portare il più possibile questo KPI vicino allo 0%. Nell’esempio qui sopra, la manutenzione correttiva ha determinato un impatto sui costi del 75% rispetto al totale speso, imputabile ad esempio al costo di consumo di materiali costosi che, probabilmente, se si fosse effettuata una buona politica di manutenzione preventiva non sarebbe stato necessario.
Peso in percentuale dell’utilizzo di risorse interne su quelle esterne
Questo KPI prevede di calcolare il peso espresso in percentuale dell’utilizzo di manodopera interna sul totale delle spese di manodopera (manodopera interna + servizi terzi).
Mediante questo parametro è possibile analizzare e decidere se spostare l’attenzione verso la terziarizzazione dei servizi oppure verso l’utilizzo di risorse interne all’azienda.
Controllo dei costi
Conclusioni
Metriche e KPIs ci permettono di fare luce sui processi di manutenzione, rendendo le le nostre azioni e le performance dei nostri assets misurabili.
Ci sono moltissimi modi in cui queste metriche possono aiutarci a ridurre il numero di fermi macchina, migliorare l’allocazione delle risorse, tagliare i costi e incrementare l’efficienza all’interno dell’azienda in cui lavoriamo.
Scegliere le giuste metriche è il primo passo sulla strada del miglioramento continuo. A seconda del nostro livello di maturazione, degli strumenti che disponiamo e degli obiettivi che abbiamo scelto, possiamo prestare attenzione a quegli indicatori che fanno al caso nostro, siano essi relativi al livello di servizio, ai nostri assets o al controllo dei costi.
Attenzione però: riuscire a monitorare nel modo corretto metriche e KPIs presuppone uno sforzo iniziale non indifferente per far sì che i dati che andremo ad analizzare siano del tutto affidabili. Disporre di un CMMS è senz’altro la via più semplice, ma almeno alcune di queste metriche possono essere monitorate anche con altri metodi e strumenti. Lo sforzo necessario sarà senz’altro maggiore, ma i benefici saranno gli stessi.
Metriche e KPI manutenzione in breve
Mean Time To Repair (MTTR)
MTTR = MTTR = Tempo totale di fermo macchina / # di fermate
Mean Time To Failures (MTBF)
MTBF = MTBF = Total Uptime / # di fermi macchina
Mean time to failure (MTTF)
MTTF = MTTF = Totale ore operative / Numero Totale di Asset in uso
Disponibilità
D = (Tempo Totale Operativo – Fermi macchina Pianificati) / Tempo Totale Operativo
Efficienza
E = [(# unità processate * Tempo ideale di un ciclo) / Tempo effettivo di processo]
Qualità del prodotto
Q = (Numero di unità conformi prodotte / Totale di unità processate) *100
Overall Equipment Effectiveness
OEE = Disponibilità * Efficienza * Qualità
Planned maintenance percentage
PMP = Ore pianificate per la manutenzione preventiva * 100 / Ore di manutenzione
Preventive maintenance compliance
PMC = PM completate / Totale PM pianificate * 100
Unisciti agli esperti
Oppure scopri il CMMS mainsim in meno di 3 minuti con questo video.