Root Cause Analysis (RCA) – Analisi delle cause radice
La Root Cause Analysis (analisi cause radice, o semplicemente RCA) è un processo sistematico per identificare le cause e le origini di un guasto, comprenderne le motivazioni e individuare le soluzioni migliori, aiutandoci a rimuovere i problemi alla radice e prolungare il ciclo di vita di impianti e apparecchiature.
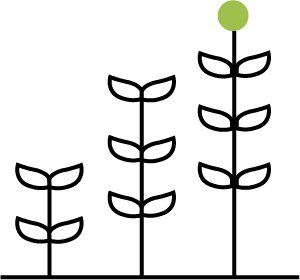
Condividi l’articolo
Contenuto dell'articolo
- A cosa serve un’analisi delle cause radice?
- Cos’è la Root Cause Analysis
- Gli obiettivi dell’RCA
- L’approccio metodologico: le sei fasi dell’analisi delle cause profonde
- Quali sono i 3 componenti della Root Cause Analysis
- Metodi comuni per l’analisi delle cause radice
- L’analisi dei 5 perché
- Il diagramma di Pareto
- Il diagramma di Hishikawa
- Il diagramma a dispersion
- Fault Tree Analysis
- FMEA
- Utilizzare un CMMS per effettuare la Root Cause Analysis
- Come implementare l’analisi delle cause radice: consigli utili
- Conclusioni
A cosa serve un’analisi delle cause radice?
Può capitare ogni tanto di sentirci fiacchi o giù di corda. La prima reazione che probabilmente avremmo ad un problema del genere potrebbe essere quella di aiutare il nostro organismo con qualche integratore alimentare in grado di rimetterci in sesto. Tuttavia, se il problema dovesse ripresentarsi, il medico potrebbe consigliarci di fare qualche analisi, per verificare quale sia l’origine effettiva del nostro malessere.
Lo stesso vale per i nostri impianti e le nostre apparecchiature. Sebbene di solito al manutentore sia richiesta una risposta immediata ad un guasto o ad un fermo macchina, un’analisi più approfondita delle cause che hanno portato al verificarsi del problema potrebbe aiutarci ad identificare le cause più profonde dietro all’orgine del guasto, identificarne gli effetti che questi eventi hanno sul processo, stabilire connessioni e, infine, individuare le soluzioni migliori per rimuovere il problema alla sua radice, anziché continuare a spegnere incendi.
Cos’è la Root Cause Analysis?
La Root Cause Analysis (RCA), in italiano conosciuta anche come Analisi delle cause radice o analisi delle cause profonde, non è altro che un processo sistematico di problem solving. Sebbene la Root Cause Analysis sia spesso impiegata in diversi campi, da quello medico fino all’amministrazione aziendale, essa assume un’importanza strategica quando si parla di manutenzione, consentendoci di comprendere le motivazioni che esistono dietro al verificarsi di un guasto, stabilire connessioni tra il verificarsi di un evento ed un altro, garantendoci così di ottenere una conoscenza più approfondita del comportamento dei nostri asset.
L’analisi delle cause profonde (Root Cause Analysis) è dunque un processo analitico e sistemico per scoprire le cause che esistono alla radice dei guasti, con l’obiettivo finale di identificare le soluzioni più aadeguati a risolvere questi problemi.
Il presupposto dietro a questo processo di problem solving e di analisi è chiaro: è molto più utile scavare in profondità un problema per trovare l’effettiva causa che lo ha generato ed evitare che si ripeta anziché continuare a curarne instancabilmente i sintomi senza fare nulla di concreto per prevenirli.
Gli obiettivi della Root Cause Analysis (RCA)
Il processo analitico alla base della Root Cause Analysis si fonda essenzialmente sulla risposta a tre tipi di domande:
- Qual è il problema?
- Perché si è verificato?
- In che modo possiamo evitare che accada di nuovo?
Per poter rispondere a queste tre domande, la RCA (Root Cause Analysis) sfrutta l’analisi dei dati che abbiamo raccolto dai precedenti guasti che si sono verificati su un determinato impianto o un’apparecchiatura.
Non stai ancora raccogliendo questi dati? Forse è il momento di pensare di portare la manutenzione dei tuoi impianti al livello pro!
Per capire meglio di cosa si tratta quando si parla di Root Cause Analysis e dei suoi obiettivi, è importante tenere sempre presente che la maggior parte dei guasti, almeno quelli più critici, sono spesso riconducibili ad altri guasti minori che, se sottovalutati o passati inosservati, possono avere ricadute disastrose sulle performance dei nostri impianti.
Anche per questo è importante riuscire ad effettuare un’analisi approfondita delle cause di guasto, attraverso, appunto, la Root Cause Analysis, al fine di comprendere in modo più completo la sequenza di eventi che hanno finito per generare il guasto.
La Root Cause Analysis, si pone in genere tre obiettivi diversi:
- Scoprire la causa principale di un guasto attraverso una diagnosi approfondita dei guasti
- Comprendere appieno come risolvere il problema e apprendere quanto più possibile da esso
- Applicare la soluzione individuata stabilendo dei processi che siano ripetibili e garantendo la loro applicazione.
Quest’ultimo obiettivo, rappresenta il punto più alto a cui un’analisi delle cause radice dovrebbe tendere: individuare le soluzioni ai problemi e automatizzarne il processo in modo da renderlo il più efficace possibile.
L’approccio metodologico: le sei fasi della Root Cause Analysis (RCA)
L’analisi delle cause radice di un guasto (RCA), si basa dunque su un approccio metodologico in cui il verificarsi di un guasto rappresenta il culmine di una serie di eventi.
In altre parole, molto spesso un guasto non è altro che la somma di una serie di altri guasti minori o condizioni sfavorevoli che, sommate l’una con l’altra, conducono al verificarsi dell’evento finale.
Ma quali possono essere le componenti principali del guasto finale? Generalmente sono da includere nell’analisi:
- Componenti ambientali
- Persone
- Attrezzature
- Materiali
- Procedure
Ancor prima di iniziare ad effettuare un’analisi delle cause profonde (RCA) è buona norma individuare quali possono essere i componenti principali della nostra indagine. Per esempio, l’ambiente in cui un determinato asset si trova ad operare, può avere effetti sul processo, sulla durata dei suoi componenti o sulle sue condizioni di lavoro? O ancora, ci sono determinate procedure, come per esempio la lubrificazione di un impianto, che se compiute regolarmente potrebbero avere un effetto positivo sugli asset aziendali?
Tenendo sempre a mente queste componenti, è possibile scomporre la procedura di analisi delle cause profonde (Root Cause Analysis) attraverso 6 fasi.
Le sei fasi della Root Cause Analysis (RCA)
- Elencare ogni possibile causa di guasto
- Raccogliere dati e informazioni precise sul processo
- Identificare le possibili cause che hanno contribuito al problema
- Analizzare i dati raccolti e individuare le possibili soluzioni
- Implementare le possibili soluzioni e valutarne gli effetti
- Implementare il nuovo piano di manutenzione
Questi passaggi sono generalmente il frutto di un processo iterativo, fino a quando le cause non sono state investigate ad una profondità sufficiente per prevenire il ripetersi del guasto. Naturalmente non è sempre un processo semplice, né immediato, per cui è necessario focalizzare l’attenzione in base al rischio in questione, alla criticità dell’evento e alla necessità di un processo di problem solving.
Quali sono i 3 componenti della Root Cause Analysis
Come abbiamo detto, molto allla radice dei guasti non vi è un solo evento scatenante, ma sono piuttosto causati da un insieme di fattori che devono tutti essere presi in considerazione quando ci si approccia ad analizzarne la causa principale.
In altre parole, il rischio di concentrarsi su di un’unica causa, individuata magari attraverso la nostra esperienza o le nostre intuizioni, può finire per limitare il set di soluzioni a disposizione, con la conseguente esclusione di alcuni approcci che potrebbero rivelarsi validi. Per questo motivo ogni volta che ci apprestiamo ad intraprendere un’indagine di problem solving attraverso la Root Cause Analysis, è necessario tenere conto di 3 componenti o cause:
- Cause fisiche: sono le cause materiali, componenti o attrezzature che hanno smesso di funzionare. Per esempio, i cuscinetti di un nastro trasportatore.
- Cause umane: sono le persone che, con il loro comportamento, hanno provocato il guasto. Generalmente, le cause umane riconducono ad una causa fisica, ad esempio l’operaio che non ha sostituito i cuscinetti del nastro trasportatore.
- Cause organizzative: si tratta di solito di errori o inefficienze nel processo di manutenzione o di conduzione di un impianto o di un asset. Ad esempio, nessuno ha sostituito i cuscinetti perché non esiste un piano di manutenzione preventiva, oppure non sono stati lubrificati perché non esiste un processo di ispezione dei componenti.
Quando ci si appresta ad effettuare una analisi RCA, è importante riuscire a prendere in considerazione tutti questi componenti, ciascuno dei quali potrebbe aver influito sul verificarsi del guasto. Si tratta, in altre parole, di non limitare l’analisi soltanto alla causa più diretta o a quella finale, ma riuscire invece ad ottenere una visione d’insieme sull’intero processo, scovando i difetti nascosti che si annidano all’interno.
Metodi più comuni per l’analisi delle cause radice (RCA)
L’obiettivo finale dell’RCA (Root Cause Analysis) è quello di identificare tutti i fattori che possono contribuire al verificarsi di un guasto. Le tecniche e i metodi per l’analisi delle cause profonde sono numerosissimi, ma nell’elenco che segue riportiamo i metodi principali e più utilizzati nella root cause analysis.
L’analisi dei 5 perché (5 why’s analysis)
L’analisi dei 5 perché (5 why’s) è forse il metodo più semplice e più utilizzato per l’analisi delle cause radice di un guasto. Resa popolare negli anni ’70 dal Toyota Production System, il metodo dei 5 perché consiste in una serie di domande che dobbiamo porci per circoscrivere il problema e indagarne in modo più approfondito la causa scatenante.
L’idea alla base di questo metodo di indagine delle cause principali è che, ad ogni perché, la risposta diventa la base per la domanda successiva.
È uno strumento di problem solving molto semplice ma anche molto utile, che non ha bisogno di statistiche avanzate e dati complessi, per cui può rappresentare un buon punto da cui partire per effettuare la nostra root cause analysis.
Ecco un esempio di analisi dei cinque perché, a partire dal caso di un mixer elettrico non funzionante.
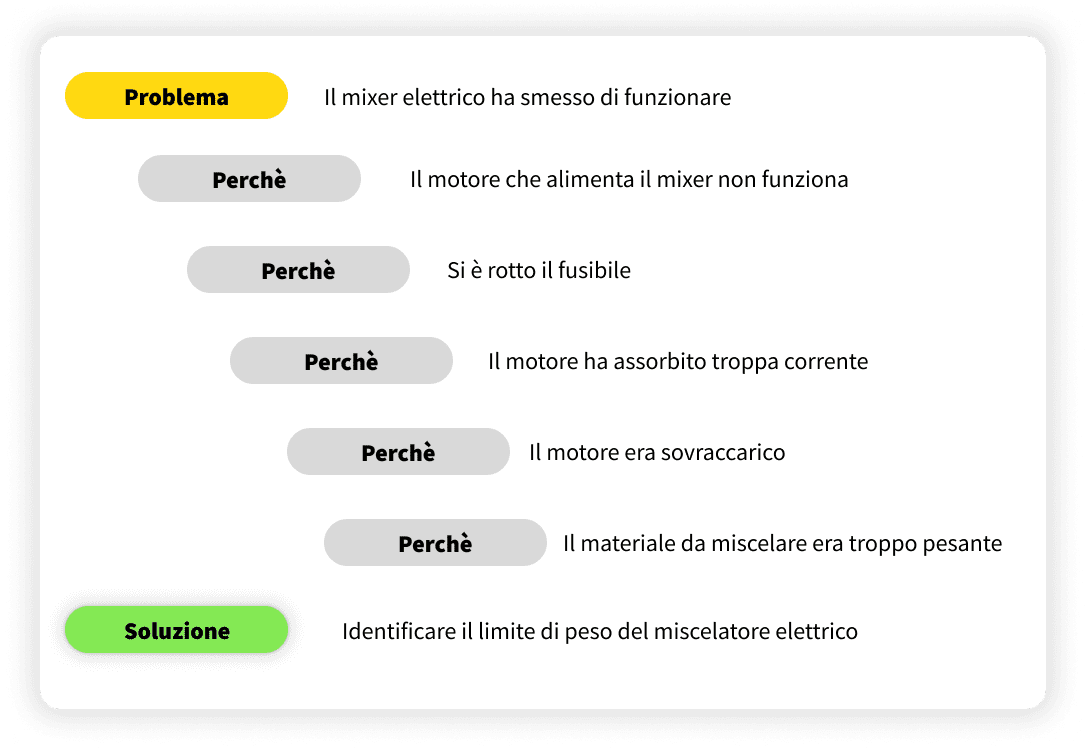
Problema: Il miscelatore elettrico ha smesso di funzionare.
- Perché? – Il motore che alimenta il mixer non funziona.
- Perché non funziona? – Si è rotto il fusibile.
- Perché si è rotto il fusibile? – Il motore ha assorbito troppa corrente.
- Perchè ha assorbito troppa corrente? – Il motore era sovraccarico.
- Perché era sovraccarico? – IL materiale da miscelare era troppo pesante
Soluzione: identificare il limite di peso del miscelatore elettrico.
Ovviamente, al fine di rendere l’indagine più completa ed accurata possibile, potrebbe essere necessario porsi più di 5 perché. L’obiettivo, è quello di individuare i problemi che si trovano all’interno del processo e rimuoverli correttamente.
Il diagramma di Pareto
Il diagramma di Pareto (o analisi di Pareto) fonda le proprie radici sulla premessa che l’80% dei problemi è prodotto da poche cause critiche (20%).
Il diagramma di Pareto consiste in un grafico a barre combinato con un grafico a linee. Le barre, mostrano con quale frequenza si verifica un evento, mentre la linea mostra il costo cumulativo o in percentuale.
Diagramma di Hishikawa (Fisbhone Diagram)
Un altro metodo molto utilizzato nella root causes analysis, è il diagramma causa-effetto, conosciuto come diagramma di Hishikawa o Fishbone diagram, a causa della sua forma a lisca di pesce. Questo metodo, derivato dal processo di gestione della qualità, permette di mappare visivamente le cause e gli effetti che un guasto ha sul processo, seguendone le diramazioni sulla base di ciascuna categoria individuata.
È una tecnica simile a quella dei cinque perché, ma segue un approccio molto più visivo, come si vede in figura.
In genere di comincia l’analisi delle cause principalia partire dal problema posto a centro del diagramma. Quindi si procede nel problem solving analizzando le varie categorie di cause, posizionate in diramazioni che si dipanano da quella principale (formando, appunto, la lisca di un pesce). Le categorie possono essere molto vaste e comprendere elementi come cause fisiche, ambientali o di processo. Una volta individuate queste categorie, continuamo a dividerle in sotto-categorie.
Mano a mano che continuamo a scavare più a fondo nelle potenziali cause e sotto-cause, analizzando ogni diramazione, ci avviciniamo sempre più alla radice del problema.
Possiamo utilizzare il diagramma di Hishikawa per eliminare le categorie che non si rivelano essere correlate al guasto, identificando invece i fattori coinvolti e le cuase profonde più probabili.
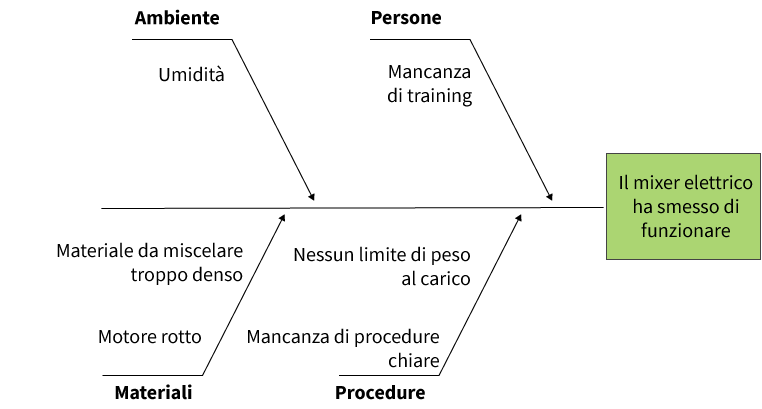
Esempio di diagramma di Hishikawa – Fishbone diagram
Diagramma a dispersione
Un ulteriore metodo per l’analisi delle cause principali di un guasto (RCA), consiste nell’utilizzo di un diagramma a dispersione. Un diagramma a dispersione ci aiuta a scoprire possibili relazioni tra variabili. Per farlo, possiamo creare un diagramma a dispersione tracciando una variabile indipendente (che rappresenta una possibile causa) sull’asse x, mentre su quella delle y andremo a posizionare la variabile dipendente (nel nostro caso, l’effetto). Se il modello mostrerà una linea o una curva ben delineata, sapremo allora che le variabili sono correlate tra loro, ed è possibile procedere alla regressione o all’analisi di correlazione.
Fault Tree Analysis
La Fault Tree Analysis, che in italiano potremmo tradurre come l’analisi dell’albero dei guasti, ci mostra visivamente quali sono gli effetti di un guasto sul nostro processo.
L’evento (nel nostro caso il guasto), viene posto alla radice dell’albero. A partire da questo, possiamo aggiungere come ramificazioni dell’albero le varie cause del guasto, analizzandole in modo maggiormente visivo.
Questo genere di analisi, richiede ovviamente una fase di brain-storming che coinvolga quante più persone possibili coinvolte nel processo.
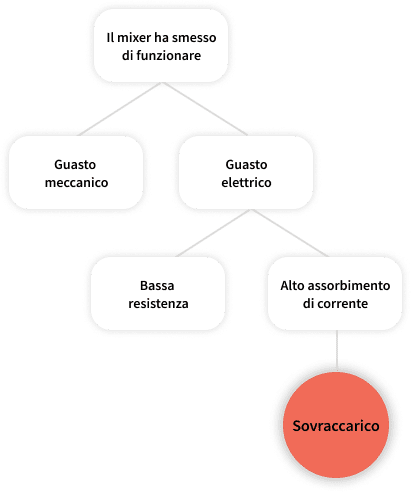
Modalità di guasto e analisi degli effetti (FMEA)
Un altro metodo pratico, molto simile alla root cause analysis ma che a differenza di quest’ultima si concentra sulla valutazione dei rischi derivanti dai guasti, è l’analisi dei guasti e degli effetti (FMEA). Questo metodo viene spesso utilizzato durante la fase di progettazione del processo per avere una visione più ampia dei potenziali difetti o dei possibili guasti.
Si tratta, in sostanza, di una semplice tabella da compilare. La tabella FMEA ci aiuta a delineare:
- Potenziali guasti, cause e conseguenze
- Controlli preventivi in grado di anticipare il problema
- Identificare la priorità di rischio
Quando viene applicato all’analisi di un processo, questo metodo prende comunemente il nome di modalità di errore del processo e analisi degli effetti, indicato dalla sigla (PFMEA).
Molti produttori di impianti e macchinari, utilizzano i risultati della PFMEA per effettuare gli audit di processo.
Utilizzare un CMMS per effettuare una migliore Root Cause Analysis
Essenzialmente, per effettuare una root cause analysis approfondita, in grado di fare luce su eventuali problemi ed inefficienze nel processo, dobbiamo quanto meno disporre di dati precisi e completi, statistiche accurate e in generale più informazioni possibile circa ogni aspetto dell’intero processo.
Ecco perché un CMMS è senz’altro la soluzione più semplice, immediata e veloce per effettuare un’analisi RCA.
Un software CMMS integra al suo interno molte funzionalità che possono fare la differenza, aiutandoti a completare l’analisi delle cause di guasto. Dai report di manutenzione fino allo storico delle attività svolte per ogni asset, tutte queste informazioni vengono automaticamente archiviate all’interno del sistema di manutenzione. Inoltre, rendendo la manutenzione più collaborativa, è uno strumento essenziale anche per migliorare la comunicazione all’interno e all’esterno del tuo team, compresi i clienti e i fornitori. Il vantaggio principale, è dunque quello di avere a portata di mano, in ogni momento, tutte le informazioni e i report necessari a completare nel modo migliore l’analisi delle cause principali.
Fig.1 – Puoi effettuare l’analisi delle cause radice direttamente sul tuo CMMS.
Alcuni CMMS di ultima generazione, vista l’importanza che assume la root cause analysis all’interno dei processi di manutenzione, integrano anche la possibilità di aggiungere dei campi ad essa dedicati agli ordini di lavoro e all’interno della dashboard di ogni asset o impianto.
Se sei già cliente di mainsim ti sarai reso conto che questo toolkit è presente all’interno del software CMMS.
Questo toolkit ti permette di semplificare la root cause analysis di ciascuno dei tuoi asset, dandoti la possibilità di inserire all’interno degli appositi campi i risultati dell’indagine relativi alla causa principale di guasto, agli effetti che ha sul processo e le soluzioni che hai individuato per correggere il problema.
In questo modo potrai creare dei template pre-compilati per i tuoi ordini di lavoro ogni qualvolta si verifichi un guasto già analizzato, oltre a check-list, immagini e documenti per aiutare i tecnici a risolvere il problema nel minor tempo possibile.
Inoltre, ti sarà più semplice controllare i risultati dell’analisi ed effettuare ulteriori indagini, aggiungendole direttamente alla dashboard dell’asset come rappresentato in figura.
Fig. 2 – Puoi aggiungere i risultati della tua root cause analysis direttamente all’interno della dashboard di ogni asset e creare template pre-compilati per gli ordini di lavoro
Conclusioni
La root cause analysis (RCA) è uno strumento potente che ci consente di identificare l’origine di un problema. Un’esecuzione efficace dei processi di analisi delle cause profonde può migliorare significativamente le prestazioni di un impianto, aiutandoti ad implementare soluzioni corrette che sono destinate a durare nel tempo.
Unisciti agli esperti
Oppure scopri il CMMS mainsim in meno di 3 minuti con questo video.
Ricevi i migliori consigli di manutenzione una volta al mese.
Unisciti agli esperti di manutenzione. Ricevi nuove risorse una volta al mese direttamente nella tua casella e-mail. E puoi annullare l’iscrizione quando vuoi.