TPM – Total Productive Maintenance
Il TPM (Total Productive Maintenance) rappresenta una strategia di manutenzione basata sull’idea che chiunque operi all’interno di una facility dovrebbe partecipare alla manutenzione di macchinari e di impianti produttivi, aiutando il team di manutenzione a svolgere il proprio lavoro nel miglior modo possibile.
In questo senso, più che una strategia di manutenzione, il Total Productive Maintenance (TPM) rappresenta una vera e propria filosofia, un approccio globale adottato da un’azienda con l’obiettivo comune del miglioramento continuo, creando così le condizioni per l’ottimizzazione del lavoro, la riduzione degli sprechi e il raggiungimento dei più alti livelli di efficienza.
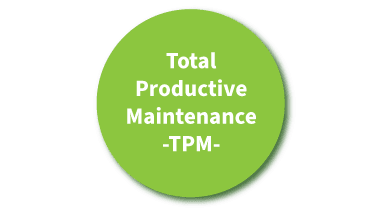
Condividi l’articolo
Contenuto dell'articolo
- TPM definizione
- TPM e il miglioramento continuo
- Obiettivi del Total Productive Maintenace TPM. Come funziona?
- 5 benefici della metodologia TPM
- TPM e manutenzione: chi dovrebbe partecipare?
- Gli 8 pilastri del TPM
- TPM e il ruolo dei dati
- Misurazione dei risultati del Total Productive Maintenance
- Costruire un programma TPM: da dove partire?
- Total Productive Maintenance esempi
TPM definizione
Con il termine TPM, Total Productive Maintenance, ci si riferisce ad un insieme di attività volte alla prevenzione e al miglioramento continuo dei processi aziendali, soprattutto attraverso il coinvoglimento degli operatori che conducono macchinari e impianti nei processi di manutenzione più semplici e che richiedono minori competenze rispetto a quelle richieste ad un manutentore vero e proprio.
TPM e il miglioramento continuo
Il TPM, come tutte le politiche di manutenzione attive, tenta di risolvere i problemi legati alla diminuzione del rendimento di macchine e impianti. L’obiettivo del Total Productive Maintenance – TPM, è dunque quello di incrementare la produttività generale attraverso l’ottimizzazione della disponibilità delle apparecchiature e dei processi coinvolti nella produzione.
La particolarità del TPM rispetto alle altre politiche di manutenzione e di analisi, come la Root Cause Analysis, risiede nel fatto che il total productive maintenance coinvolge l’intera azienda, ad ogni livello. Questo è un fatto fondamentale per comprendere l’importanza del TPM e di come esso possa ridurre sprechi, evitare guasti, perdite di produttività, ridurre l’impatto ambientale e molto altro, in quello che viene definito un processo di miglioramento continuo.
Spesso però si incorre in un equivoco molto comune: quello di considerare il TPM come una metodologia legata unicamente alla manutenzione di macchine e impianti. Non è così. Il Total Productive Maintenance è un processo in grado di coinvolgere tutti gli aspetti e i ruoli relativi alla conduzione aziendale.
Il concetto stesso di manutenzione produttiva, nasce negli Stati Uniti con lo sviluppo dell’aviazione civile (lo stesso ambiente in cui nascono anche i software di manutenzione CMMS). Viene poi approfondito e sviluppato in Giappone da Seiichi Nakajima (lo stesso teorico che ha fondato il concetto di OEE – Overall Equipment Effectiveness e stabilito il World Class Standard). Oggi, gli stessi concetti vengono impiegati all’interno della maggior parte delle aziende mondiali.
Obiettivi del Total Productive Maintenance TPM. Come funziona?
Il TPM (Total Productive Maintenance) poggia le sue fondamenta sul metodo 5S (di cui parleremo in modo più approfondito più avanti in questo articolo). Senza entrare troppo nei dettagli, per il momento, ci basti sapere che la metodologia 5S è una filosofia legata al lean manufacturing che aiuta le aziende a creare delle procedure standard per raggiungere obiettivi che sono sia di produzione che di qualità ed efficienza. Oltre a le 5S, esistono altri sette pilastri del TPM, così come teorizzati dallo stesso Nakajima.
Li affronteremo in modo dettagliato nei prossimi paragrafi. Ma prima, vediamo insieme quali sono i principali benefici derivanti dall’applicazione della metodologia di manutenzione TPM.
5 benefici della metodologia TPM
Gli obiettivi principali del TPM Total Productive Maintenance sono:
- Riduzione degli interventi di manutenzione non pianificati: Attraverso un’attenta pianificazione della manutenzione programmata, è possibile incrementare sensibilmente il ciclo di vita dei nostri assets ed evitare – oltre ad arresti inaspettati – anche piccole perdite di produttività dovute a micro fermate non ascrivibili in veri e propri fermi macchina e di cui non è sempre semplice tenere traccia se non con un software manutenzione CMMS o EAM.
- Riduzione dei fermi macchina: Incrementando il numero di interventi pianificati, di manutenzione programmata e di manutenzione preventiva conducono ad una diminuzione del numero di fermi macchina veri e propri. Implementando strategie di manutenzione proattiva, guasti e fermi macchina sono ridotti al minimo.
- Riduzione dei costi di produzione: Migliorando l’OEE (Overall Equipment Effectiveness) i costi di produzione si riducono. Un incremento della produzione conduce a profitti più alti e riduce le spese dovute ai fallimenti dei macchinari e ai tempi di riparazione, oltre a quelli di rilavorazione dei prodotti non conformi agli standard stabiliti dall’azienda.
- Miglioramento della sicurezza sul lavoro: Dal momento che il TPM poggia sul metodo 5S, il luogo di lavoro deve essere sistematicamente organizzato e pulito (Straight e Shine sono le due S coinvolte, ma lo vedremo meglio tra poco). Ciò è importante per migliorare l’efficienza del team di manutenzione, scoprire nuove problematiche e assicurare un ambiente adatto al lavoro.
- Ottimizzazione delle risorse: A partire dal team di manutenzione, il TPM permette di coinvolgere tutta l’azienda all’interno dei processi di manutenzione, liberando risorse in modo tale che i tecnici possano concentrarsi su interventi manutentivi per cui sono richieste maggiori competenze.
TPM manutenzione: chi dovrebbe partecipare?
Come già accennato all’inizio di questo articolo, nella filosofia TPM, chiunque all’interno di un’azienda essere partecipe dei processi di manutenzione, a partire dal top management fino agli operai che lavorano ad un determinato impianto. Ognuno, infatti, è chiamato a portare il proprio contributo.
- Top management: Nel concetto stesso di TPM, il management dovrebbe essere coinvolto promuovendo, oltre ad un cambiamento culturale (assolutamente necessarie per un corretto approccio al Total Productive Maintenance), anche tutte quelle attività propedeutiche al miglioramento continuo, attraverso l’imposizione di una vera e propria policy aziendale che ne tenga di conto. Inoltre, attraverso l’analisi dei dati registrati e organizzati tramite un software CMMS, si possono generare importanti metriche e stabilire KPIs il cui monitoraggio può fornire preziosi insights sui nostri processi produttivi e di manutenzione.
- Operatori: Tecnici e operatori sono coloro che lavorano più assiduamente ad un macchinario o ad un impianto. Per questo motivo dovrebbero essere responsabili per le operazioni giornaliere effettuate sul macchinario, come per esempio la pulizia o la lubrificazione necessarie per garantire la salute dell’impianto. Inoltre, è ragionevole aspettarsi che siano proprio loro i primi a cogliere segnali di malfunzionamento o di deterioramento e segnalarli al reparto di manutenzione.
- Responsabili della manutenzione, supervisor e tecnici: Queste figure hanno la responsabilità della manutenzione degli asset aziendali. È necessario dunque il monitoraggio continuo di metriche e indicatori (come per esempio il MTBF – Mean Time Beteween Failure, o il MTTR – Mean Time To Repair). Il monitoraggio di queste metriche rappresenta un aspetto fondamentale per il miglioramento continuo, poiché rende possibile elaborare, scegliere e perfezionare le strategie manutentive più efficaci per ogni asset, aumentando la loro disponibilità ed efficienza (e quindi anche i livelli di produzione) nel pieno rispetto dei principi da cui muove la filosofia TPM.
Gli 8 pilastri del Total Productive Maintenace (TPM)
Il TPM (total productive maintenance) mira dunque alla massimizzazione della capacità produttiva di macchine e impianti attraverso un processo di miglioramento continuo volto alla riduzione degli sprechi e delle perdite che possono verificarci durante le varie fasi di produzione.
In particolare Nakajima individua 8 pilastri su cui si fondano i valori e le operazioni necessarie per adottare e implementare correttamente il total productive maintenance all’interno di un’azienda.
Vediamoli nel dettaglio.
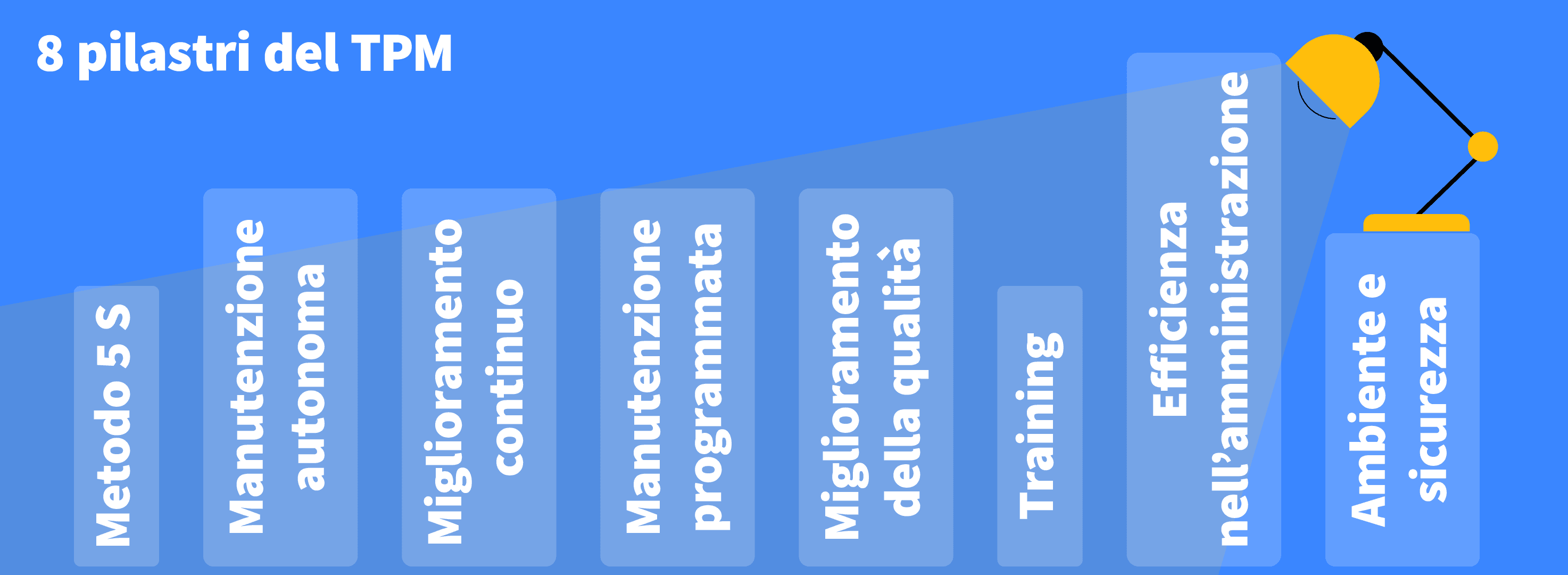
1) Le 5S (e la lean production)
Come accennato in precedenza, alla base della filosofia TPM (total productive maintenance) sta il metodo 5S. Ma cos’è e quali sono le 5S?
In primis può essere utile chiarire come le 5S rientrino perfettamente nelle logiche di lean production e lean manufacturing volte a snellire i processi di produzione ottimizzandoli in un processo di miglioramento continuo.
Detto ciò, dovrebbe essere chiaro a tutti il motivo per cui il metodo 5S rappresenti uno e forse il primo dei pilastri del TPM.
Inoltre, è bene precisare come, per loro stessa natura, le 5S riguardino principalmente azioni che possono compiere gli operatori addetti ad un macchinario o ad un impianto, anziché il team di manutenzione.
Vediamo nello specifico quali sono le 5S:
- Sort (Sgomeberare): La prima delle 5S consiste nel riuscire a classificare gli strumenti di lavoro in modo tale da identificare quelli che hanno bisogno di essere sostituiti.
- Straighten (Sistemare): Garantire una postazione di lavoro ordinata, in cui gli strumenti che verranno utilizzati con maggiore frequenza siano facilmente raggiungibili rappresenta la seconda delle 5S che, per praticità, abbiamo tradotto con il verbo sistemare, o mettere in ordine.
- Shine (Splendere): La terza delle 5S riguarda la pulizia della propria postazione di lavoro. Significa pulire accuratamente e in modo sistematico la propria postazione.
- Standardize (Standardizzare): Standardizzare e pianificare le attività sopra elencate rappresenta la quarta delle 5S, con la quale – in sostanza – si precisa che le operazioni precedenti devono necessariamente diventare una procedura sistematica per ogni operatore che lavora ad un impianto.
- Sustain (Sostenere): La quinta delle 5 S si riferisce alla necessità di supportare il processo nel lungo termine. Senza tale costanza, infatti, ogni sforzo compiuto sarebbe vanificato prima ancora di dare risultati tangibili.
L’approccio 5S consiste dunque nella pulizia dello spazio di lavoro, nell’organizzazione della strumentazione disponibile in modo tale da mettere gli operatori nella posizione di poter svolgere il proprio lavoro nel miglior modo possibile e identificare più facilmente possibili problematiche (sempre nell’ottica del miglioramento continuo).
2) Manutenzione Autonoma
Piccoli interventi di manutenzione possono essere effettuati direttamente dall’operatore addetto ad un macchinario o impianto. Ciò permette da una parte di responsabilizzare gli operatori stessi (valore necessario per l’adozione di logiche e metodi di manutenzione TPM) e dall’altra di ridurre il carico di lavoro del team di manutenzione, lasciandolo libero di concentrarsi su quelle problematiche che richiedono maggiori competenze. Rientrano in questo pilastro e nella manutenzione autonoma, non solo la rilevazione di piccoli guasti e micro-fermate ma anche la cura dell’impianto per quelle piccole opere di manutenzione ordinaria come per esempio la lubrificazione.
3) Miglioramento continuo
Il miglioramento continuo rappresenta indubbiamente uno dei pilastri più importanti del TPM. Tramite piccoli miglioramenti ai processi è possibile infatti ottenere risultati tangibili in termini di efficacia dei nostri impianti e macchinari, in modo molto più semplice che attraverso complesse strategie di manutenzione.
4) Manutenzione Programmata
Le attività di manutenzione programmata sono essenziali per prevenire fermi macchina e arresti inaspettati. Una politica di manutenzione programmata, fatta periodicamente, può migliorare sensibilmente le condizioni di assets, macchine e impianti, prevenendone il deterioramento.
5) Miglioramento della qualità
Il quinto pilastro del TPM riguarda la qualità del prodotto. L’obiettivo è quello di identificare ogni possibile causa che conduca alla produzione di parti che non siano conformi agli standard di qualità. La qualità del prodotto è un aspetto fondamentale dei processi di produzione, coinvolto anche nel calcolo di altre metriche di monitoraggio come l’OEE (Overall Equipment Effectiveness). Infatti, come è logico che sia, gli scarti di produzione rappresentano un’inefficienza dei nostri impianti e dei processi, che porta alla necessità di rilavorazioni e perdite di produzione che talvolta possono essere anche importanti.
6) Training
L’idea alla base della manutenzione TPM è che ognuno collabori all’efficienza generale del processo di produzione. Per raggiungere obiettivi di performance ottimali, è necessario infatti formare e addestrare il proprio team in modo tale che tutti acquiscano il know-how necessario da mettere in pratica al momento opportuno.
7) Efficienza nell’amministrazione
Un ruolo chiave nel total productive maintenance, talvolta però sottovalutato, è quello svolto dall’amministrazione. Eppure, sarebbe impossibile implementare una filosofia orientata al TPM senza il necessario contributo del management, chiamato in questo caso a promuovere in modo attivo il cambiamento necessario a coinvolgere le parti e soprattutto nella responsabilizzazione delle figure aziendali che dovranno svolgere attività che in qualche modo esulano dal loro compito principale (basti pensare alla manutenzione autonoma da parte degli operatori addetti ad un impianto).
8) Ambiente e Sicurezza
L’ultimo degli otto pilastri della manutenzione TPM concentra l’attenzione sulla creazione di un ambiente di lavoro sicuro.
Total productive maintenance e il ruolo dei dati
Uno degli aspetti fondamentali del Total Productive Maintenance (TPM) è la necessità di avvalersi del rilevamento di dati e della diagnosi delle entità da manutenere. La possibilità, infatti, di registrare e monitorare i dati relativi alle performance di macchinari e impianti rappresenta uno degli aspetti chiave per il miglioramento dell’efficienza e dell’efficacia degli stessi. Ogni qualvolta si parla di manutenzione preventiva e di manutenzione programmata (uno dei pilastri, come abbiamo visto, del TPM) è infatti necessario poter fare affidamento sui dati per decidere dove e quando allocare risorse ed evitare di incorrere in eccessi di manutenzione che vanificherebbero gli sforzi compiuti.
Alcune tra le metriche più comuni che dovremmo monitorare in modo continuativo sono:
- Mean Time Between Failure (MTBF)
- Mean Time To Failure (MTTF)
- Mean Time To Repair (MTTR)
- Overall Equipment Effectiveness (OEE)
Inoltre, e non in ordine di importanza, un software di manutenzione CMMS o EAM permette agli operatori che conducono una macchina o un impianto di segnalare alla direzione guasti e anomalie incorse, ma anche di avvalersi in modo semplice e veloce di checklist per la manutenzione autonoma, oltre alla disponibilità di dati e di uno storico degli interventi effettuati sulla macchina in modo tale da semplificare il lavoro e aumentare la produttività.
Misurazione dei risultati del total productive maintenance – TPM
Il TPM è uno strumento di particolare interesse per quelle aziende produttive ad alta intensità di capitale, in cui il costo degli impianti produttivi risulta necessariamente più rilevante.
L’obiettivo finale del TPM è quello di accorciare i tempi di consegna per fornire prodotti di alta qualità ad un costo minore. Ciò è reso possibile grazie alla capacità di snellire i processi, eliminando sprechi e ogni tipo di attività che non apporti alcun valore alla produzione.
Non esiste però una metrica specifica, valida per la misurazione del TPM. Essendo però il Total Productive Maintenance volto al miglioramento dei livelli di produzione, possiamo rifarci a metriche che misurano la produttività aziendale. Il più comune di questi è senz’altro l’indicatore OEE (Overall Equipment Effectiveness) il quale permette di individuare un numero indice (espresso in %) della produttività aziendale.
Costruire un programma TPM: da dove partire?
Muovendo dai pilastri sopra descritti, possiamo pensare ad un programma (o almeno un inizio) che sia in grado di mettere in pratica la metodologia TPM nel modo corretto.
Ma da dove partire?
Il primo punto assolutamente imprescindibile è il fattore culturale che deve coinvolgere l’intera azienda a partire dal top management. Senza questa condizione, potrebbe essere molto complesso trasferire il necessario know-how a tutti i dipendenti, mettendo ognuno nella condizione di dare il proprio contributo richiesto.
Detto questo, non vi è alcun dubbio sul fatto che la base di partenza, il primo pilastro da cui partire, sia quello delle 5S. L’obiettivo, deve essere quello di creare un processo standard che sia alla base delle attività giornaliere di chi conduce le macchine/impianti.
Una volta consolidato questo processo come insieme di operazioni da compiere giornalmente, potremo procedere con l’introduzione dei successivi pilastri del TPM così come elencati in precedenza.
La manutenzione autonoma, il secondo pilastro del total productive manitenance, è evidentemente legato a quello delle 5S. Riguarda tutte le attività di pulizia, ispezione, di identificazione dei fattori che possono contribuire al deterioramento delle macchine/impianti. Può essere utile avvalersi di una checklist, cartacea o digitale (questo dipende dal livello di digitalizzazione dell’azienda) e fissare standard chiari e precisi di pulizia, ispezione e lubrificazione.
Raggiunti questi primi obiettivi che sono quelli fondanti le metodologie TPM, avremo ancora molto lavoro da compire, ma potremo essere certi di aver già raggiunto i primi e più importanti traguardi, gettando le basi per l’implementazioni dei successivi pilastri del TPM.
Total Productive Maintenance esempi
L’esempio classico quando si parla di TPM, è quello di Toyota. Non è un caso infatti che lo stesso Nakajima (padre del TPM e molto altro) sia stato a lungo il direttore tecnico della casa automobilistica giapponese.
Le prime esperienze di TPM in Italia furono invece quelle di FIAT.
Unisciti agli esperti
Oppure scopri il CMMS mainsim in meno di 3 minuti con questo video.
Ricevi i migliori consigli di manutenzione una volta al mese.
Unisciti agli esperti di manutenzione. Ricevi nuove risorse una volta al mese direttamente nella tua casella e-mail. E puoi annullare l’iscrizione quando vuoi.