Time-based maintenance: come utilizzare al meglio la manutenzione basata sul tempo
La manutenzione basata sul tempo (in inglese: time-based maintenance) è una delle strategie più utilizzate dai Responsabili della manutenzione.
Dopotutto, è anche la tipologia di manutenzione preventiva più semplice da attuare.
In molti casi basta rifarsi alle indicazioni prescritte dal produttore di un macchinario, fissare le date sul calendario e il gioco è fatto.
Se questo è il tuo modus operandi, sappi che forse non la stai sfruttando al meglio.
Affinché una manutenzione basata sul tempo sia efficace, deve essere utilizzata su attrezzature che presentano modalità di guasto legate all’età. Ma ci sono molti studi che dimostrano come questa non sia una condizione comune e che anzi, la maggior parte dei guasti non sono affatto legati all’età di un’attrezzatura o di un componente.
In altre parole, i nostri programmi di manutenzione preventiva non dovrebbero essere basati esclusivamente sul tempo.
In questo articolo prendiamo in considerazione 4 studi piuttosto importanti. Ora, c’è una buona possibilità che tu abbia effettivamente letto o sentito parlare di almeno uno di questi ai tempi dell’università: infatti, nonostante alcuni di essi siano un po’ datati, restano comunque molto attuali e vengono menzionati spesso nei programmi di ingegneria meccanica e industriale.
- UAL 1968 è uno studio condotto dalla United Airlines (Nolan e Heap) tra gli articoli fondanti la Reliability-Centered Maintenance.
- Broberg 1973 è un altro studio che porta avanti la ricerca di Nolan e Heap, giungendo alle stesse conclusioni sulla distribuzione dei modelli di fallimento.
- MSP 1982 è uno studio condotto dalla Marina degli Stati Uniti.
- SUBMEPP 2001 è lo studio più recente citato in letteratura, anche questo condotto dalla Marina americana sui propri sottomarini.
Cos’hanno in comune questi studi? Tutti e quattro dimostrano che la maggior parte delle modalità di guasto non sono legate all’età.
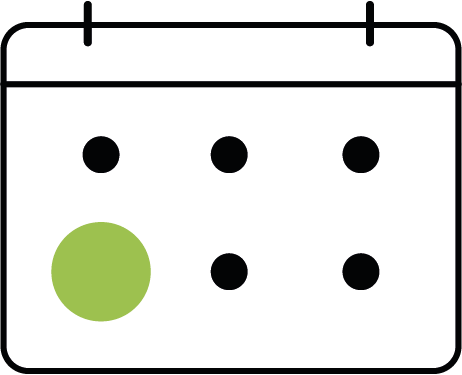
Pattern e distribuzione dei guasti
Molto probabilmente conosci già la curva a vasca da bagno come pattern per la distribuzione delle cause di guasto.
In questo grafico proviamo a mettere insieme diversi pattern di guasto e la loro distribuzione in base a quanto riportato negli studi che sono stati citati sopra.

Ok, il grafico è un po’ complesso, per cui lasciami provare a spiegarlo meglio.
Nella prima colonna sono riportati i modelli di fallimento identificati da Nolan e Heap nel loro studio sull’RCM.
I primi 3, il modello A, B e C sono legati all’età, D e E sono modelli casuali, mentre il discorso è un po’ più complesso per l’ultimo modello (F).
Il modello F infatti potrebbe rientrare nella distribuzione dei guasti così detta a Mortalità infantile, per ciò in qualche modo legata al tempo. Tuttavia Nolan e Heap non considerano questo modello come correlato al tempo, poiché dopo un momento iniziale si assiste ad una rapida caduta della probabilità di guasto, la quale resta più o meno costante (a differenza del modello A).
Le colonne successive invece riportano la distribuzione corrispondente ad ogni modello così come evidenziata dai diversi studi.
Prima di andare avanti con l’analisi però, vorrei fare un breve disclaimer per chiarire un punto importante: come dicevo all’inizio, questi studi sono stati condotti prevalentemente nel settore aeronautico o in quello navale. Perciò dovremmo considerare fattori tipici, come per esempio il fatto che la mortalità infantile è di solito più alta negli aerei, o come un ambiente particolarmente corrosivo come l’acqua marina possa generare un numero maggiori di guasti legati all’età.
Tuttavia non credo sia questo il punto. Ciò che mi preme sottolineare di questo grafico è come, in generale, una larga percentuale di modalità di guasto non sia effettivamente legata all’età come – al contrario – verrebbe spesso da pensare.
In effetti, secondo i modelli proposti, la probabilità di guasto resta costante per la maggior parte del tempo. E cioè, la maggior parte dei guasti si verifica in modo casuale.
Come si traduce tutto questo nei nostri piani di manutenzione preventiva?
Tutto ciò dovrebbe essere tenuto in considerazione quando si stilano i nostri piani di manutenzione preventiva. Perché se la maggior parte dei guasti non è legata all’età, allora dovremmo pensare di inserire nei nostri piani un qualche tipo di valutazione basata sulle condizioni, anziché esclusivamente sul tempo.
Ovviamente questa non è una regola aurea, ma dovremmo farci almeno qualche domanda quando spendiamo buona parte del nostro budget nella manutenzione preventiva ma non vediamo miglioramenti sostanziali. Perché non c’è niente di peggio che continuare ad aggiustare qualcosa che poi continua a rompersi.
Come utilizzare la manutenzione basata sul tempo in modo efficace.
Quanto detto finora non è altro che la doverosa premessa per il tema centrale di questo articolo: la manutenzione basata sul tempo è una perdita di denaro?
La risposta è molto semplice: no.
Il problema è che troppe organizzazioni fanno ricorso ad una manutenzione basata sul tempo (time-based maintenance) in modo improprio o eccessivo all’interno dei loro piani di manutenzione.
E questo fatto rischia di compromettere tutto il lavoro svolto perché rappresenta:
- uno spreco di denaro
- uno spreco di tempo e risorse
- una perdita di produzione o di produttività
Aggiungo che questo fatto è in buona parte alla radice della fatidica, eterna lotta tra manutenzione e produzione.
E già questo dovrebbe dirla lunga sulla sua importanza…
Nei prossimi paragrafi faremo un paio di esempi molto semplici descrivendo il diverso scenario che si incontra tra una manutenzione basata sul tempo e una manutenzione su condizione.
Prima però, permettimi di contestualizzare meglio cos’è e cosa si intende per time-based maintenance.
Cos’è la time-based maintenance?
Quando parliamo di time-based maintenance o di manutenzione basata sul tempo, viene naturale contrapporla alla manutenzione basata sulle condizioni o tutt’al più alla manutenzione basata sul rischio.
Ma cos’è davvero la time-based maintenance?
La manutenzione basata sul tempo si riferisce ovviamente ad un’attività manutentiva svolta ad intervalli fissi, prendendo come variabile principale – appunto – il tempo o il tempo di utilizzo, indipendentemente dalle sue condizioni effettive.
Dove sta il problema con questo tipo di manutenzione?
Non essendo correlata alle condizioni di un componente o di un articolo (come per esempio l’olio lubrificante di un motore), il problema principale è lo spreco, perché prevede la sostituzione del suddetto componente/articolo prima del suo normale fine vita.
Ciò può avere senso, soprattutto nel caso in cui si abbia a che fare con un componente a basso costo, una lavorazione particolarmente rapida da effettuare o un guasto potenziale senza conseguenze importanti. Ma in altri casi rappresenta uno spreco di cui potremmo fare decisamente a meno.
In effetti, la manutenzione basata sul tempo è davvero efficace soltanto quando ha a che fare con modalità di fallimento che sono correlate all’età, come nel modello qui sotto:

Quando ci troviamo di fronte ad un’attrezzatura per cui vale ad esempio un modello come questo sopra, sappiamo che l’asset oggetto di manutenzione inizia a degradarsi ad un certo punto. Al tempo T, la probabilità di guasto aumenta rapidamente.
Il problema ovviamente è sapere quando il nostro intervento si rende necessario (cioè il tempo T nel grafico).
Anticipare troppo l’intervento non ci consentirebbe di utilizzare a pieno il ciclo di vita del componente, fermare un impianto quando ancora non è davvero necessario, etc.
Posticipare l’intervento invece… beh, o siamo fortunati o qui entriamo nel mondo della manutenzione a guasto. Potrebbe andarti bene, oppure finire per essere un vero disastro.
Time-based Vs Condition-based: 2 esempi a confronto
Esempio 1. Olio lubrificante
Il primo esempio che voglio fare riguarda un articolo molto comune: l’olio lubrificante.
Domanda:
Siamo nel campo della manutenzione basata sul tempo o sarebbe meglio invece adottare un approccio basato sulle condizioni?
Meglio sostituire l’olio lubrificante ogni due anni, ogni 15mila chilometri o ogni 4mila ore?
Per quanto riguarda questo genere di articoli, è pratica comune quella di adottare una manutenzione basata sul tempo.
In effetti, se ragioniamo sulle potenziali modalità di guasto, come la contaminazione con sporco o acqua, queste non sono di solito legate all’età.
Lo stesso vale per il suo degrado (per esempio degli additivi che contiene): certo, è presente anche una componente temporale, ma molto dipende da altri fattori come la temperatura o il carico di lavoro.
Mettiamo allora le due strategie di manutenzione a confronto:
A) manutenzione basata sulle condizioni:
La modalità di guasto è decisamente casuale, motivo per cui molte aziende prima di sostituirlo effettuano spesso controlli e analisi, rendendo questo approccio molto simile ad una manutenzione su condizione.
Effettui un controllo, un’analisi dello stato dell’olio e decidi il da farsi. Questo approccio è vantaggioso per due motivi: primo perché così facendo puoi gestire meglio eventuali modalità di guasto impreviste e casuali, secondo perché generalmente puoi allungare il tempo di utilizzo dell’olio fino a quando non è effettivamente esausto.
B) manutenzione basata sul tempo:
L’esempio sopra è valido soprattutto quando si parla di macchinari industriali che consumano enormi volumi di olio lubrificante.
Se gestisci una flotta di mezzi da strada, come automobili, che necessitano di quantità di olio piuttosto ridotte, probabilmente non troverai un grande risparmio adottando una strategia come sopra e con ogni probabilità sarà più vantaggioso invece perseguire un approccio conservativo.
Esempio 2. Filtri
Come per l’esempio precedente, anche per i filtri (per esempio i filtri dell’olio motore) la questione potrebbe risultare ambigua.
A) manutenzione basata sul tempo:
In genere i filtri per l’olio motore sono un componente che si installa velocemente, per cui ha senso sostituire il filtro indipendentemente dalle condizioni. Mettiamo una volta al mese. Certo, potresti misurare la pressione differenziale attraverso il filtro per valutarne le condizioni effettive, ma ne varrebbe la pena?
B) Manutenzione basata sulle condizioni:
Cosa succede però se si dispone di filtri di processo, più costosi e di grandi dimensioni? Probabilmente hai decine e decine di elementi filtranti installati e cambiarli richiede tempo e lavoro.
In questo caso potresti trovare più vantaggioso limitare il numero di filtri sostituiti fintanto che le loro prestazioni restano adeguate.
Per fare ciò sarà necessario installare un kit di misurazione e monitorare l’andamento della pressione differenziale, in modo da condurre un’attività di sostituzione dei filtri basata sulle condizioni.
In questo caso potresti trarre un beneficio maggiore abbandonando il tuo programma di manutenzione basata sul tempo, perché rischi di eseguire una manutenzione eccessiva, incorrendo in costi aggiuntivi che probabilmente non portano alcun vantaggio concreto.
Time-based maintenance: Tiriamo le somme
Quando si parla di manutenzione preventiva non esiste un one fits all.
Per riuscire a rendere più efficaci ed efficienti i nostri programmi abbiamo bisogno di considerare diversi fattori, che vanno dalle modalità di guasto ai costi, fino all’effort che richiedono certi interventi, con l’obiettivo finale di trovare il giusto mix.
Nella maggior parte dei casi però la scelta non è così semplice.
Molte aziende sono ancora troppo orientate ad un approccio correttivo (a guasto) e quando finalmente decidono di migliorare i propri programmi inserendo elementi di manutenzione preventiva commettono spesso l’errore di buttarsi a capo fitto in un approccio time-based semplicemente perché si tratta della scelta più semplice. Dopotutto, è sempre meglio di niente, giusto?
In effetti ci sono pro e contro per entrambi gli approcci.
Per esempio, la manutenzione basata sul tempo richiede certamente un effort minore rispetto alla on-condition, poiché le condizioni degli asset vanno monitorate con maggior regolarità e potrebbero richiedere anche costi extra, come per esempio l’acquisto o il monitoraggio di contatori.
D’altra parte se la manutenzione su condizione potrebbe farti risparmiare montagne di denaro evitando guasti, perdite di produzione e fallimenti molto impattanti sul business, potrebbe rivelarsi anche uno spreco inutile.
Per prendere una decisione sensata in merito è necessario conoscere bene i nostri asset.
Ecco alcuni strumenti, metriche e KPI che potrebbero aiutarti a prendere decisioni informate e stabilire con maggior serenità quando conviene adottare un approccio anziché un altro:
- MTBF (Mean Time Between Failures): calcola il tempo medio che intercorre tra un guasto e l’altro. Se stai già adottando un approccio basato sul tempo, potrebbe aiutarti a comprendere meglio se c’è un legame con l’età di un componente.
- Storico degli interventi: avere un database aggiornato dei guasti ti aiuta ad identificare pattern di guasto e comprendere meglio il funzionamento dei tuoi asset. Ci sono guasti che si verificano con maggior regolarità di altri?
- Analisi delle cause di guasto (RCA): La root cause analysis è una delle attività più importanti per analizzare le cause di guasto, gli effetti generati (conseguenze) e le soluzioni adottate, attraverso un unico strumento. Tuttavia, può essere un po’ complicata da portare avanti senza un solido sistema di raccolta e analisi dati come un CMMS.
- Costo per asset: l’analisi dei costi relativi ad un asset e ai guasti che intercorrono ci consente di fare chiarezza sull’opportunità di adottare un approccio anziché un altro.
- Trend MTBF Vs Manutenzione preventiva: questa metrica ci aiuta a verificare la bontà dei nostri piani di manutenzione. A differenza dell’MTBF, analizzare il trend in relazione alle attività di manutenzione preventiva ci aiuta a capire in che modo questa metrica è correlata alle nostre azioni programmate, verificandone l’efficacia.
- MTTF (Mean Time To Failure): quando ci si concentra su componenti che anziché venir riparati solitamente vengono sostituiti, non avrebbe senso monitorare l’MTBF. Al suo posto, possiamo prendere in considerazione il tempo medio al verificarsi del guasto (MTTF).
- Trend Manutenzione Correttiva Vs Manutenzione Pianificata: il monitoraggio di questo trend ci aiuta a capire se, e in che modo la manutenzione pianificata porta ad una riduzione effettiva dei guasti.
Condividi l’articolo
Contenuto dell'articolo
- Pattern e distribuzione dei guasti
- Come utilizzare la manutenzione basata sul tempo in modo efficace
- Cos’è la time based maintenance
- Time-based maintenancee e Condition-based: 2 esempi a confronto
- Time-based maintenance: conclusioni
Vuoi continuare ad informarti?
Ecco altri contenuti simili
Unisciti agli esperti
Oppure scopri il CMMS mainsim in meno di 3 minuti con questo video.