Contarina: manutenzione su condizione e gestione della flotta per oltre 500 mezzi
Contarina S.p.A. ha adottato un sistema di manutenzione su condizione per il proprio parco mezzi, abilitando un approccio data-driven che ottimizza tempi di fermo, disponibilità e gestione dei ricambi.
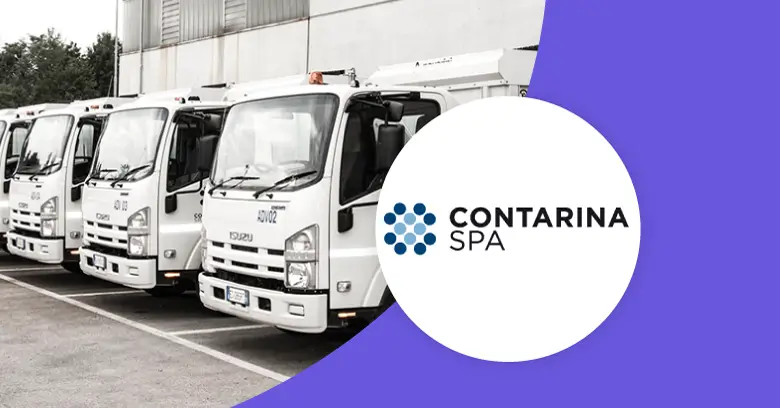
SETTORE
servizi ambientali
cosa gestisce
fleet management
mezzi gestiti
+550
-62%
Mezzi fermi al mese
-75%
Riduzione ore di straordinario
degli addetti
-7%
Riduzione dei costi di manutenzione/mese
Obiettivi del progetto
Manutenzione on-condition
Digitalizzare i dati di manutenzione
Ottimizzare i fermi dei veicoli
Integrare officina e magazzino
Monitorare KPI e performance
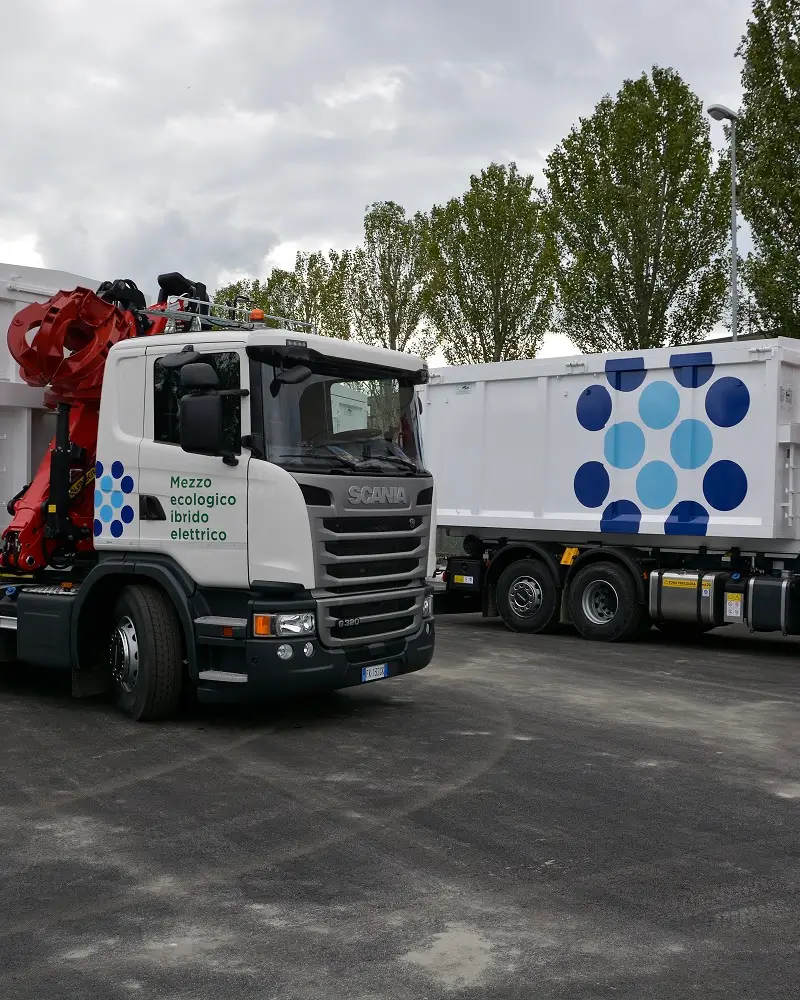
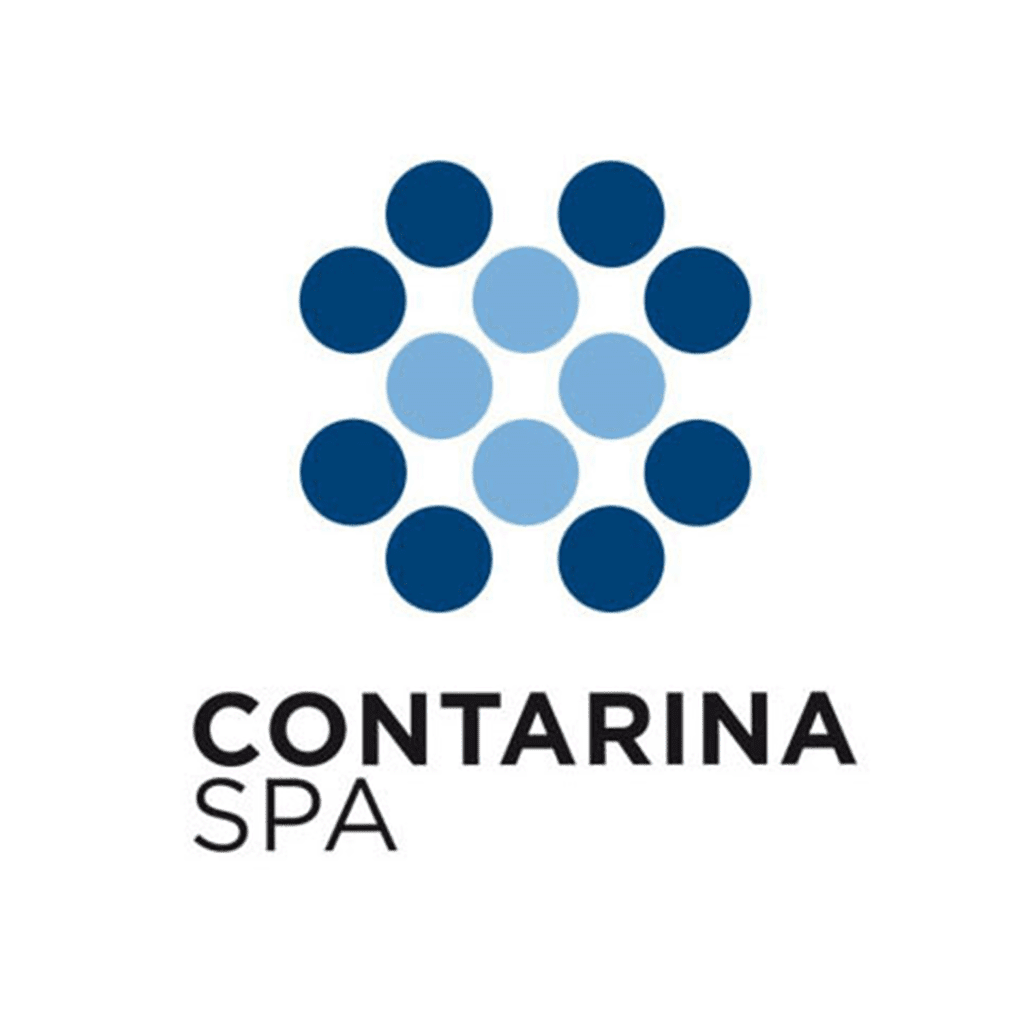
“Vox populi: mainsim ci ha cambiato la vita.”
Sergio Ricci, Vice Direttore Generale, Contarina S.p.A.
Al vertice della gestione ambientale con una flotta sempre operativa
Contarina S.p.A. è una società a completa partecipazione pubblica attiva nella gestione dei rifiuti e nei servizi ambientali. Fondata nel 1989, l’azienda si posiziona ai vertici europei per risultati nella raccolta differenziata ed è considerata un modello virtuoso nella gestione sostenibile del territorio.
Con una flotta operativa di oltre 500 mezzi e quasi 800 risorse attive, Contarina gestisce un servizio complesso e capillare, in cui efficienza e continuità operativa sono fondamentali.
Per questo motivo, la digitalizzazione dei processi di manutenzione e l’integrazione tra officina, magazzino e sistemi gestionali rappresentano asset strategici per garantire affidabilità e qualità del servizio pubblico.
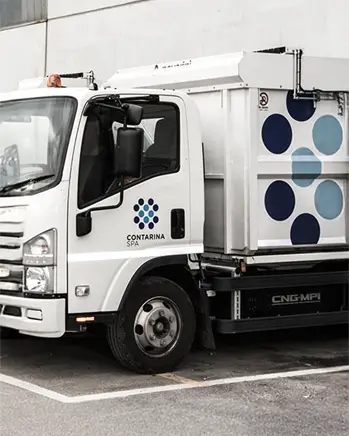
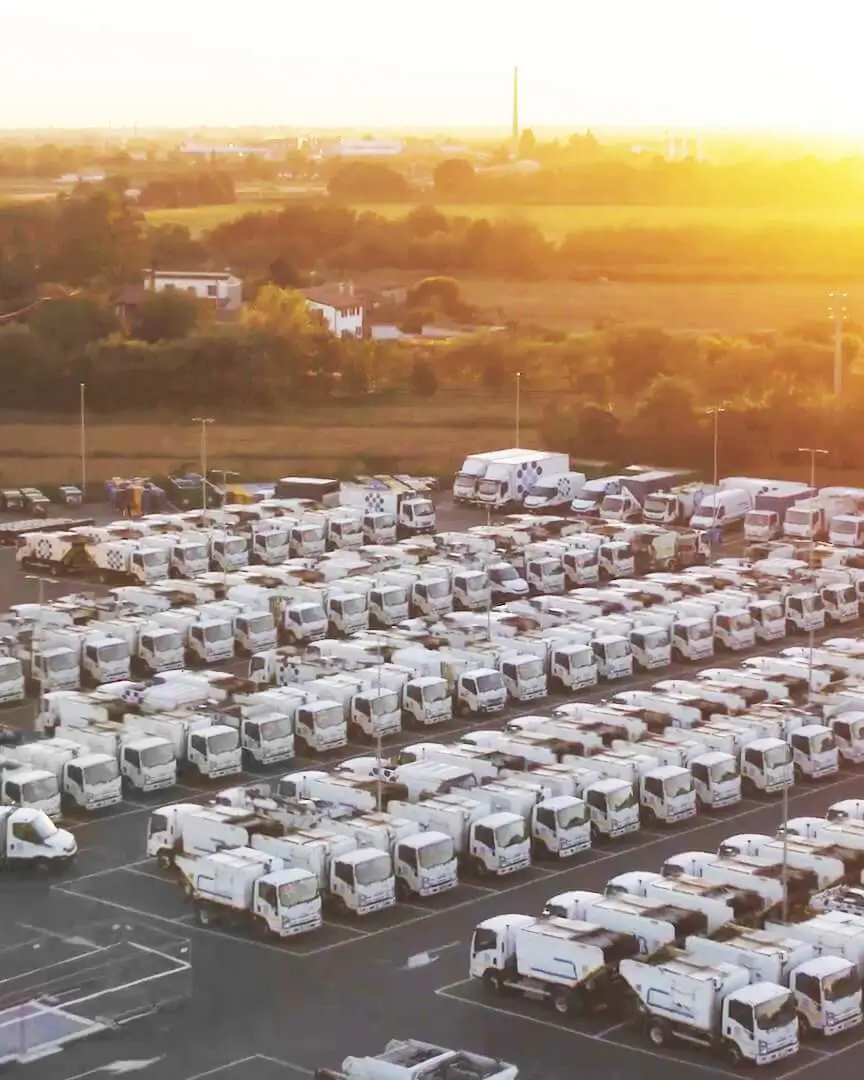
Dalla gestione su carta alla manutenzione on-condition
Prima dell’adozione di mainsim, Contarina S.p.A. gestiva la manutenzione con sistemi cartacei e dati non strutturati, con forti limiti in termini di tracciabilità, analisi e ottimizzazione. La digitalizzazione del processo ha permesso di trasformare l’intero flusso in un sistema automatizzato e reattivo, in cui ogni attività è guidata da dati aggiornati in tempo reale.
Grazie all’integrazione con il gestionale Ecos, il sistema acquisisce in automatico i chilometri percorsi dai mezzi e genera ordini di lavoro non appena vengono raggiunte le soglie previste per i tagliandi. La logica di manutenzione su condizione è ulteriormente potenziata da una gestione dinamica: il CMMS è in grado di valutare se sulla base dei chilometri percorsi siano imminenti manutenzioni preventive e in tal caso anticiparle, evitando così ulteriori fermi ridondanti. In questo modo, ogni intervento viene sfruttato al massimo, riducendo l’impatto operativo e aumentando la disponibilità del parco mezzi.
La stessa logica di integrazione viene applicata alla gestione del magazzino: i ricambi vengono tracciati tramite barcode, scaricati automaticamente dalle giacenze e collegati direttamente agli ordini di lavoro. I tecnici operano da mobile, registrando tempi e attività in tempo reale tramite la funzione Rec&Stop, riducendo le attività manuali e migliorando l’affidabilità dei dati raccolti.
Infine, la proiezione visiva del modulo Kanban e la reportistica avanzata supportano il monitoraggio costante dei KPI e l’analisi delle cause di guasto (RCA), per una manutenzione realmente evoluta e basata sui dati.
“Proprio come un’azienda produttiva, la disponibilità degli asset deve essere sempre assicurata per evitare pericolose perdite di produttività, con tutti gli effetti negativi ad essa associata.”
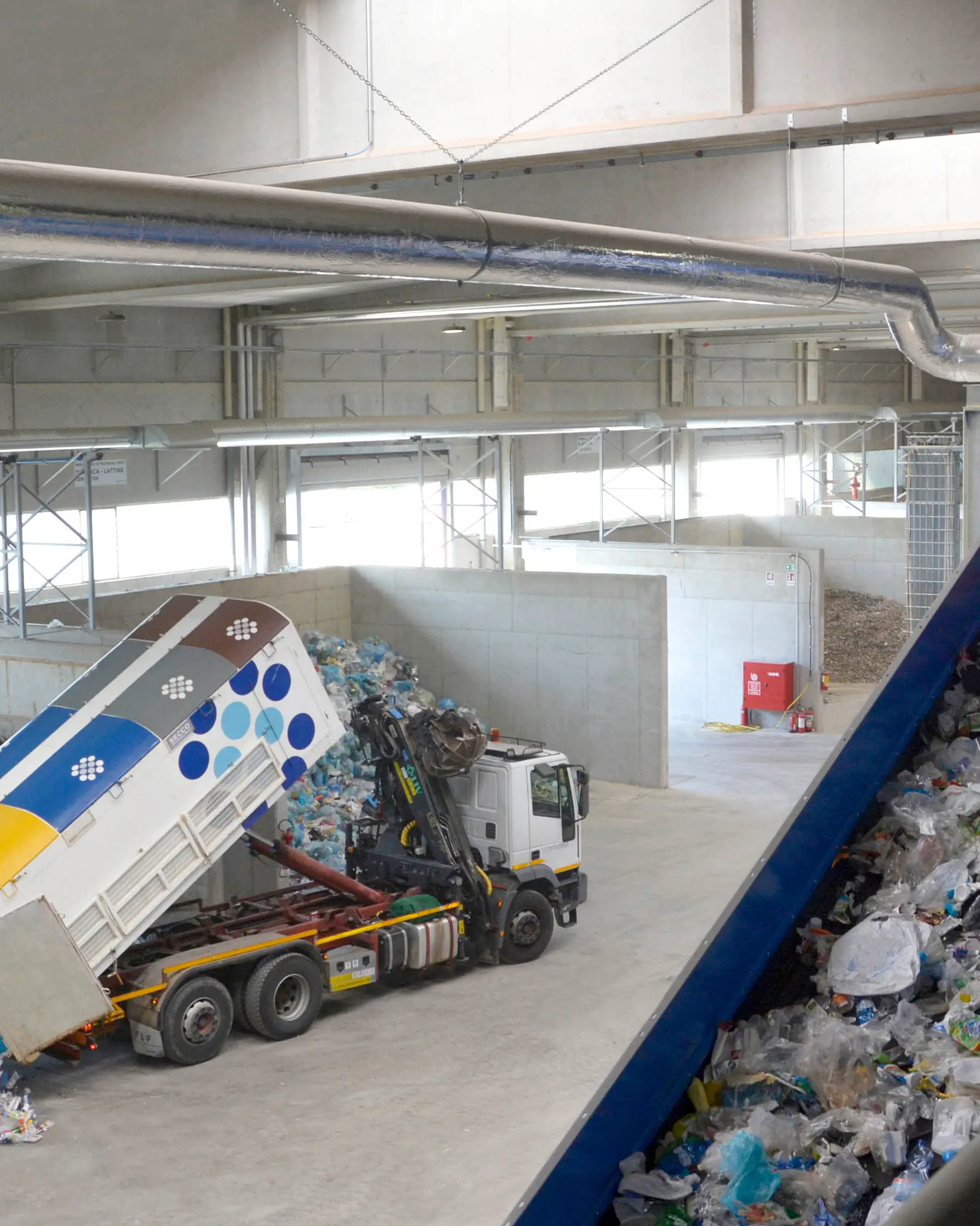
Sei in cerca di ispirazione?
Guarda altre storie di successo simili.
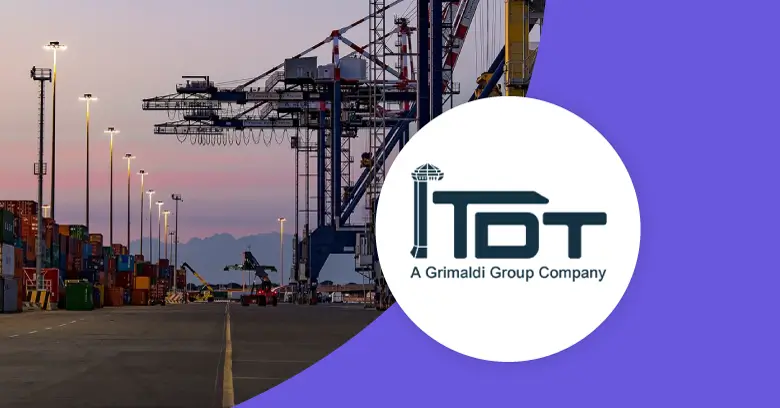
Terminal Darsena Toscana
Manutenzione On-Condition e Time-based per gli asset di movimentazione in banchina.
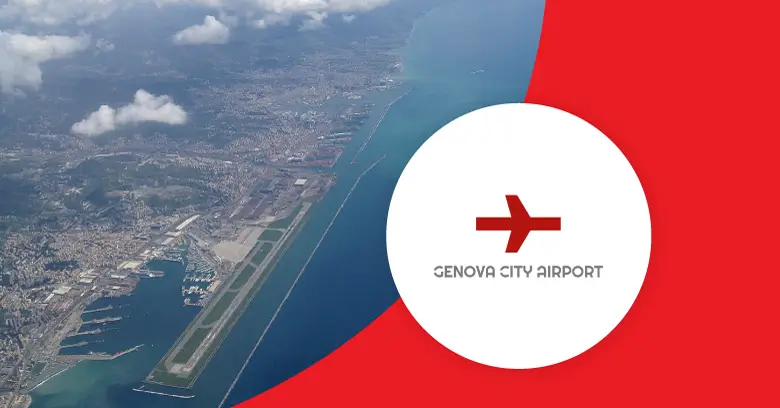
Aeroporto di Genova
Migliorare l’efficienza delle operazioni a terra attraverso la gestione dei mezzi critici.
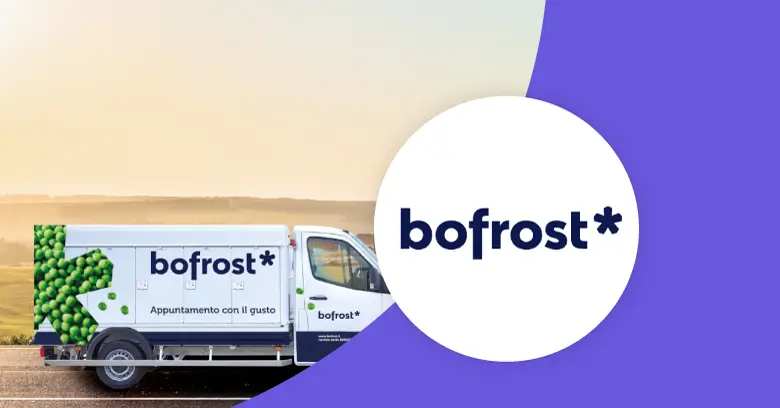
Bofrost
La gestione degli asset critici con focus sulla catena del freddo e sulle strutture specializzate.
Mettici alla prova.
Valutiamo insieme le tue sfide, ti spieghiamo come il CMMS Mainsim è in grado di aiutarti e ti aiutiamo a mettere in pratica il cambiamento.
Non sei ancora pronto per una demo? Scarica la brochure